LSR technology
A further machine on display will be an all-electric EcoPower 110/350 LIM with the new B8X control system used to demonstrate Wittmann Battenfeld’s expertise in liquid silicone processing. With this machine, four different closing caps for beverage cans and bottles will be produced from liquid silicone in a single injection-molding process, using a 4-cavity mold from Nexus, Austria. The open design of the EcoPower’s injection unit enables easy integration of the LSR metering unit. The Nexus X200 metering unit comes with a new Servomix dosing system and is connected with the machine’s B8X control system via Euromap 82.3 OPC-UA integration. In the mold, latest cold-runner technology with Flowset needle shut-off regulation is used. The parts are removed by a Wittmann W918 robot and packaged by a flow wrapping machine.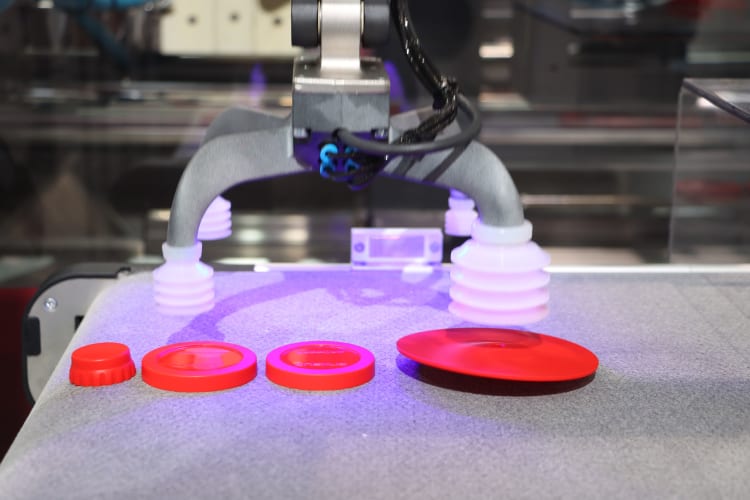
Automation and auxiliaries
In addition to the robots and auxiliary appliances connected to the machines on display, numerous robots and auxiliaries from Wittmann will also be shown as stand-alone solutions at the Plast in Milan.From its range of automation equipment, Wittmann Battenfeld Italia will show a WP80 sprue picker, a W918 robot with R9 control system, a model from the low-cost PRIMUS series, a Primus 48T, and a Sonic 108 high-speed robot. The Sonic 108 is the latest high-speed parts removal appliance from Wittmann, developed for clamping forces ranging from 500 to 1,500 kN. The typical cycle time of this robot model is below 4 seconds for gripper weights of up to two kg.
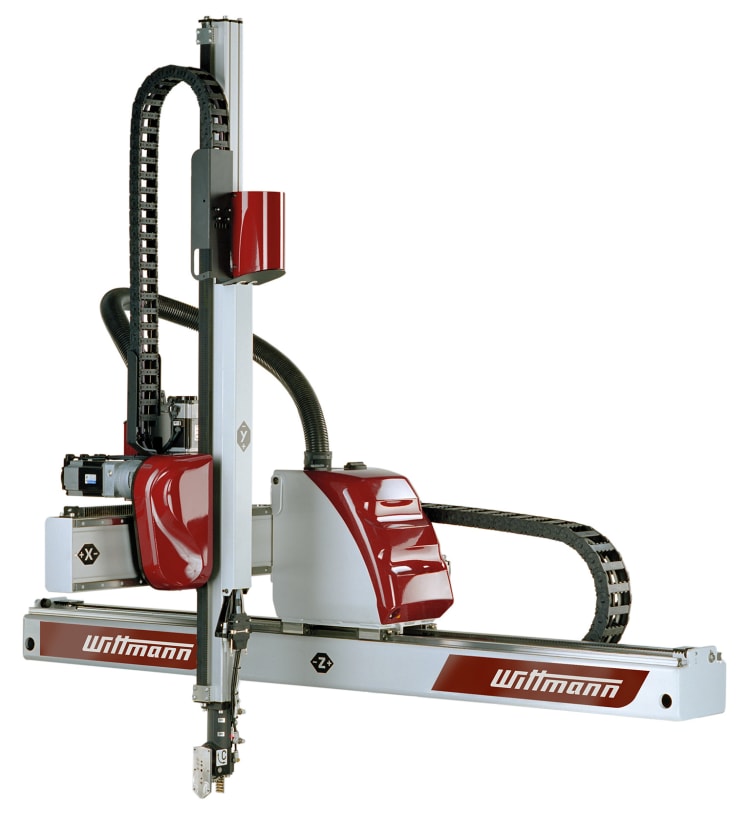
Wittmann Battenfeld Italia will also present an extensive portfolio of Wittmann auxiliaries to Plast visitors.
Some of these exhibits will be a Wittmann central material conveyor system, plus a Feedmax S3 standalone loader, a Dosimax MX12 volumetric blender and a Gravimax 14 gravimetric blender.
From its range of dryers, Wittmann Battenfeld Italia will showcase Drymax plus 30 dry air dryers and drying batteries consisting of Drymax and Silmax batteries, as well as a Codemax coupling station. The program will be rounded off by an Aton plus segmented wheel dryer and a Card primus compressed air dryer with a VacuJet conveyor for material throughputs of up to 120 kg per hour.
In addition to a wall showing various types of flow controllers, Wittmann temperature control technology will be represented by the temperature controller models Tempro basic C90, C120 and C140, as well as a Tempro plus D two-circuit appliance. The Tempro plus D appliances come with a self-explanatory touch display for easy operation. Numerous options are available to configure these appliances for virtually all applications found in plastics processing.

Exhibits from the Wittmann Group’s granulator range will be one S-Max 1 and one S-Max 2 screenless granulator, and a G-Max 9 granulator. G-Max granulators are energy-efficient and come with a small footprint as well as a sound-insulated cutting chamber. The S-Max granulators feature toothed rollers with low motor speeds (27 rev/min at 50 Hz) for efficient, low-cost granulating of engineering plastics as well as styrene, acrylic and fiberglass-reinforced materials.
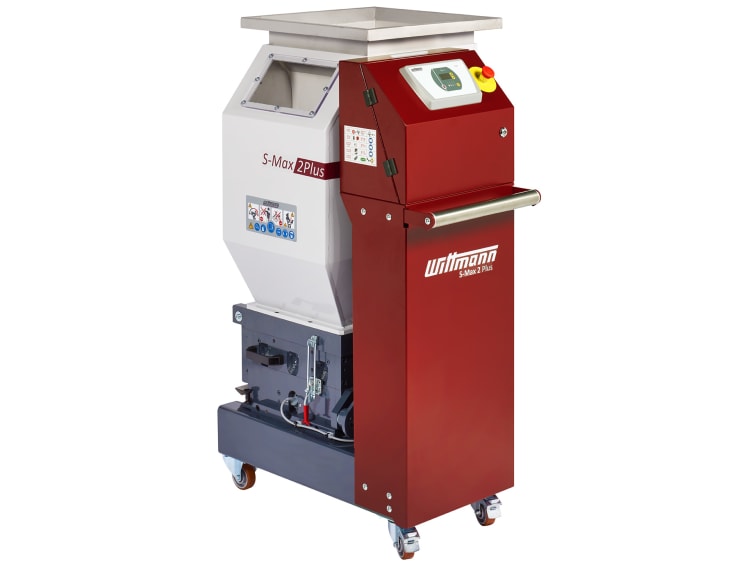
In addition, visitors to the Plast will have the opportunity to familiarize themselves with the Wittmann Battenfeld Airmould 4.0 internal gas pressure technology and the Wittmann 4.0 digitization solution at special “expert points” provided for this purpose.
Latest developments in TEMI+ and IMAGOxt
At the Plast, Wittmann Digital will introduce its Temi+ Academy and its Imagoxt peak control system.
The Temi+ Academy is a new service to enable managers and operators to fully exploit the potential of the Temi+ Mes system with the help of an extensive training program.
Another novelty to be presented by Wittmann Digital at the fair is the Imago peak control system, a "lite" version of the Imago system destined to help companies avoid energy consumption peaks. With its intuitive user interface and real-time dashboards, the Imago peak control system enables companies to achieve seamless, efficient optimization of their energy consumption. By identifying potential peak times and providing real-time warning signals, it becomes possible to make well-founded decisions about the energy consumption, and about shifting various loads by appropriate demand management strategies. The Imago peak control system will enable companies not only to improve their energy efficiency, but to contribute to a more sustainable future as well.