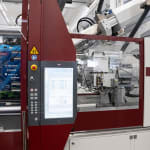
From 5 to 8 September 2023, Wittmann Battenfeld will present to visitors of the Plast Milan at its booth No. 121/122 in hall 22 energy-efficient injection molding machines combined with ultra-modern process technology and complex automation systems, as well as the latest robots and auxiliaries from Wittmann.
The Italian market is one of the Wittmann Group’s most important export markets. Consequently, the Plast Milan is a major platform for Wittmann to present its state-of-the-art technologies jointly with its local subsidiary, Wittmann Battenfeld Italia S.r.l. Its second Italian subsidiary, Wittmann Digital S.r.l., specializes in digital solutions for the plastics industry and is also using the Plast as an ideal stage for launching its latest developments in the areas of Temi+ manufacturing execution systems and the Imagoxt energy consumption analysis tool.
The injection molding machines on display will be servo-hydraulic models from the SmartPower and SmartPrimus series, plus one all-electric machine from the EcoPower series. The SmartPrimus, formerly known as SmartPlus, originates from the SmartPower series. This machine stands out by its high level of cost and energy efficiency as well as repeatability. Using the well-proven SmartPower technologies in combination with a choice of optional extras makes it possible to offer an excellent price-performance ratio for this machine series.
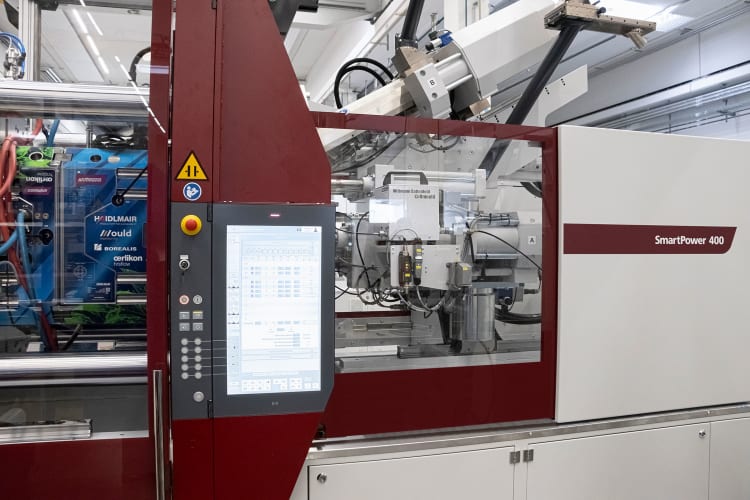
Multi-component and light-weight technology
With the production of a re-usable 3-component coffee-to-go cup with lid on a SmartPower 400/750H/210S/525L Combimould, visitors will be given an insight into the company’s expertise in multi-component technology, as well as Cellmould light-weight technology. The machine is equipped with a rotary unit and a mold supplied by Haidlmair, Austria. The material to be used for manufacturing both the cup and the lid is Bornewables from Borealis. Bornewables consists entirely of renewable materials (i.e., non-petroleum-based feedstock) and is both food safe and dishwasher safe. The feedstock for making Borealis Bornewables originates from bio-mass, waste and residual substances of the second generation, which are not in competition with the human food chain. The mold from Haidlmair is laid out optimally for processing Bornewables material. A special feature of this mold is the use of hybrid elements in the mold plate to optimize cooling.The cup produced in clear optic in the first cavity is over-molded in the second cavity with a shell and provided with an additional insulating effect by foaming the melt with Cellmould technology. The lid for the cup is injection-molded in an adjacent cavity. It consists of the same material as the main body, but can be individually colored thanks to the special mold technology. The parts are removed and deposited on a conveyor belt by a WX142 robot, then passed on to a flow wrapping machine and packaged. The packaging material used in this instance also comes from the Bornewables product family from Borealis.
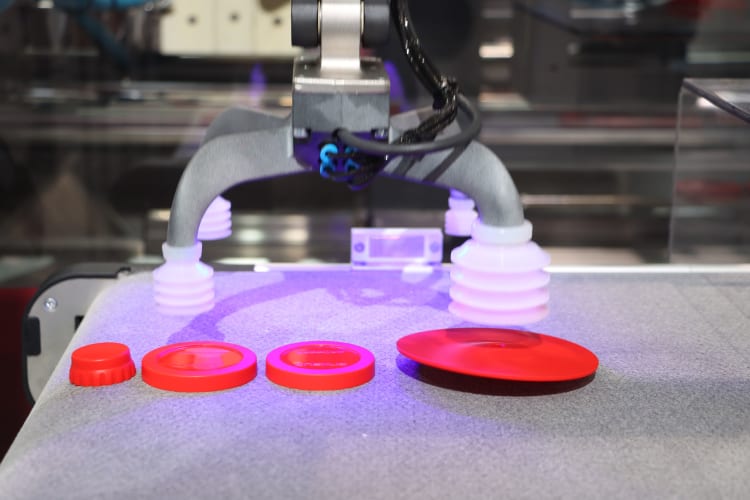
Digitization and automation
Wittmann Battenfeld will demonstrate its expertise in digitization and automation at the Plast in Milan by manufacturing a spirit level on a SmartPrimus 90/350 with the new B8X control system.The machine comes with the CMS Lite condition monitoring system from Wittmann and a special automation cell designed and constructed by Wittmann Battenfeld Germany. With a 1+1-cavity mold supplied by SOLA, Austria, the spirit level will be produced from ABS. As a first production step, the top and bottom parts of the spirit level housing are injection molded. The top part is then deposited and printed at a laser station. Simultaneously, the bottom part placed on a tray is fitted with vials from SOLA. Next, the top part is pressed onto the bottom part by a pre-set force. The finished parts are then transported to a testing station, where the positioning of the vials is checked by a vision system. After quality inspection, the finished spirit levels are removed and deposited on a conveyor belt by a WX138 robot from Wittmann.
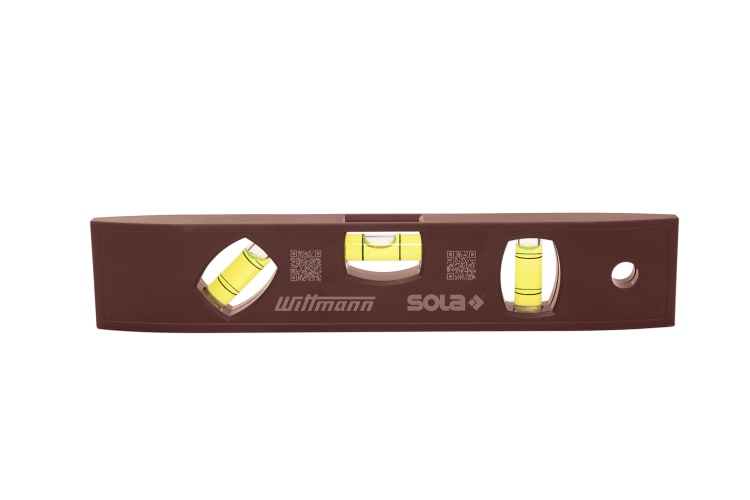