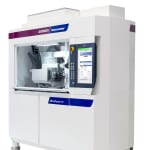
Since Fakuma 2020 has been postponed to next year due to the health risks arising from the SARS-CoV-2 virus, Wittmann Battenfeld has decided to present the exhibits originally planned for the Fakuma and several other interesting applications in the form of product videos, and post them on a “Virtual Fakuma” portal.
Presentation of the videos will take place primarily in personal meetings with customers; web conferences are also planned as an alternative. To present the product highlights as vividly as possible to a wide public, the product videos will also be made available on the company’s YouTube channel.
An innovation: the Ingrinder
With the Ingrinder, Wittmann Battenfeld has created an innovative solution to promote the recycling economy. This product is an injection molding system with integrated sprue picker, granulator and vacuum conveyor. The granulator and the sprue picker can be operated via the machine’s UNILOG B8 control system.
Wittmann Battenfeld presents this innovation on a machine from the servo-hydraulic SmartPower series, a SmartPower 60/210. On the machine, a can with a lid is produced from PS with a 2-2-cavity mold. A WP50 sprue picker from Wittmann with swivel drive removes the sprue and passes it to the G-Max granulator integrated in the system. The material recycled by the granulator is then transported to the machine’s material hopper by a FEEDMAX basic vacuum conveyor. The Wittmann vacuum conveyors enable alternating conveyance of virgin material and regrind, so that a thorough blend is created by this process, together with discharge of the material into the hopper.
High-speed EcoPower Xpress for the packaging industry
Another highlight that Wittmann Battenfeld will demonstrate to its existing and prospective customers is a machine from the EcoPower Xpress series. This EcoPower Xpress is an all-electric, high-speed and high-performance machine model primarily of interest for thin-walled applications in the packaging industry. An EcoPower Xpress 300/1100+ equipped with the new Wittmann SONIC 131 top-entry robot will be shown. This robot can be used for applications with a robot cycle time from 4 s. With a mold supplied by Abate, Italy, this machine will produce a margarine tub from PP within a cycle time of 4 seconds.
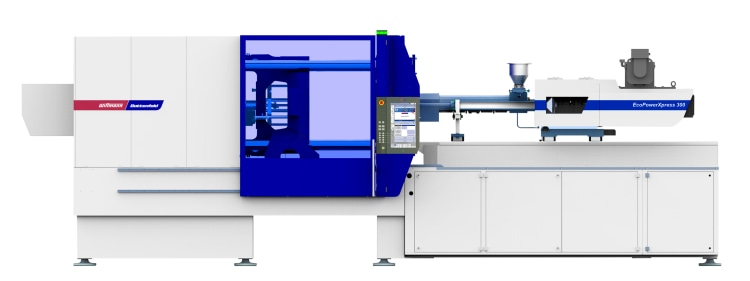
Medical application on MicroPower 15/10 production cell
Moreover, Wittmann Battenfeld will demonstrate its expertise in the field of medical technology with a machine from the MicroPower series conceived for the production of micro parts in a clean room version. Using a MicroPower 15/10 with 150 kN clamping force, a micro retaining ring for medical miniature tubes will be produced from PC with an 8-cavity mold supplied by Wittner, Austria. This product has a part weight of only 2 mg.
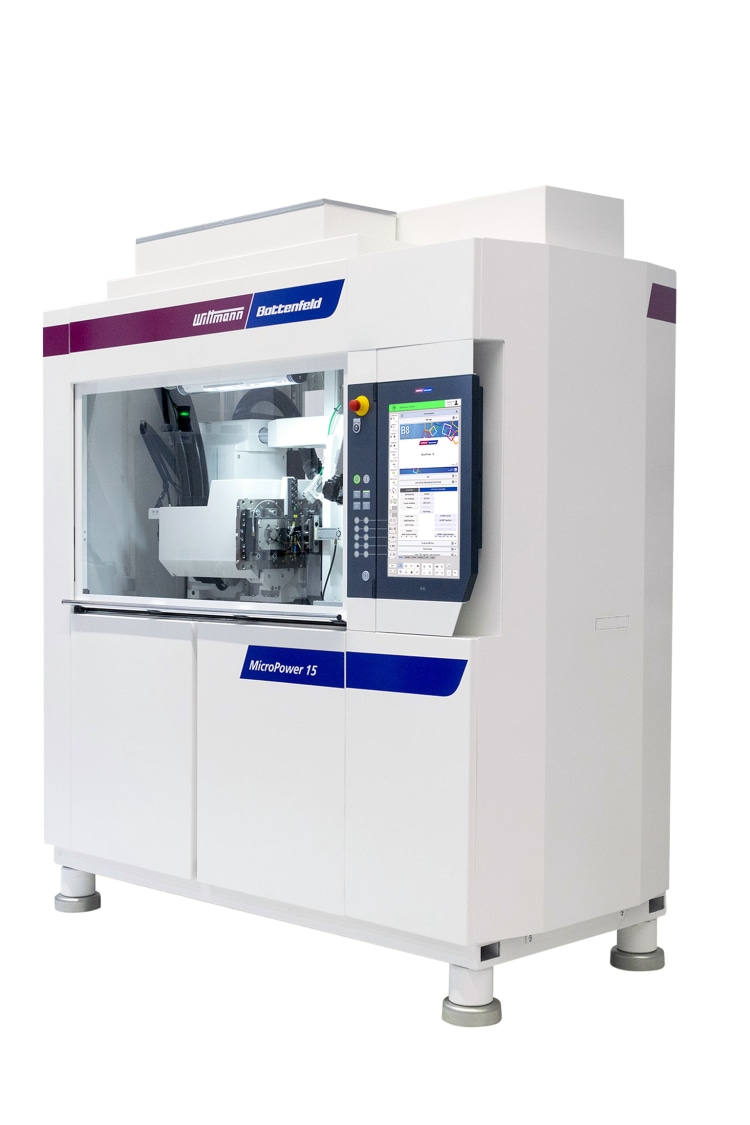
The machine comes with a rotary unit, an integrated Wittmann W8VS2 robot and a camera for complete parts inspection. Following removal and camera inspection, the parts are transferred to transport containers, separated according to individual cavities.
LSR application on SmartPower 120
The important Wittmann Battenfeld technology for LSR processing is presented by producing a drink timer made of LSR on a machine from the servo-hydraulic SmartPower series, a SmartPower 120/350, with a 2-cavity mold supplied by Nexus, Austria. The injection unit in open design enables easy integration of the LSR metering unit. The Nexus Z200 metering unit comes with a new servomix metering system with OPC-UA integration. In the mold, latest cold runner technology is used including FLOWSET needle shut-off control. Parts removal and depositing will be handled by a W918 robot from Wittmann.
Completely updated integrated MES TEMI+
All Wittmann Battenfeld machines can be connected to the MES solution TEMI+ from ICE-flex. TEMI+ is specifically designed and optimized for the needs of the plastics industry and provides advanced OEE calculations and data integration of molding machines via Euromap 63 or 77, as well as auxiliary equipment via Wittmann 4.0/OPC UA. The new version of TEMI+ comes with a completely new HMI engine, a powerful Production Planner and the optional IMAGOxt package for graphical measurements such as energy consumption.
Although the frontend HMI has only undergone minor modifications from previous versions, the underlying framework technology is entirely new, allowing for fast operator interaction and highest stability. The updated Production Planner however has changed significantly in the new version, enabling intuitive additions and shifting of production jobs via drag & drop, an extended planning of maintenance cycles and an easy-to-understand weekly job agenda. The optional IMAGOxt package creates graphs for energy or material consumption. Actuators and alarm responses can be programmed directly from the TEMI+ interface.