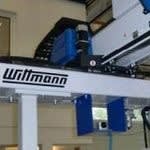
In its approach to development, Wittmann Battenfeld focuses primarily on stable and optimal parts quality. This is why the company acquired the worldwide usage rights for the inline thermography process developed by SKZ (Das Kunststoff-Zentrum) in Würzburg, Germany. Wittmann Battenfeld is presenting this process to the professional visitors at Fakuma 2011 in Friedrichshafen.
Inline thermography is a process for identifying quality variations, shot for shot, associated with the regulation of temperature control when tolerances are exceeded. This makes it possible to avoid rejects and ensure stable parts quality. This “quality assurance in the hot state” is achieved by recording surface temperatures of an injection molded part with a thermographic camera immediately after the ejection process.
For this purpose, the linear robot presents the part to the camera in various positions immediately after ejection. Then the software developed by SKZ evaluates the temperature profile. Deviations from the ideal temperature profiles are calculated and segment-dependent corrections are sent to the cooling circuits of the mold via the Wittmann Flowcon flow regulation unit connected to it. That means any necessary temperature changes are implemented in real time.
One major advantage of this process is the external temperature measurement on the ejected component. As a result, the specific mold used requires no modifications or additions.
By contrast to conventional temperature measurement with thermal sensors inside the mold, thermographic measurement on the molded part offers a number of significant advantages:
The camera systems used are considerably more accurate and robust than thermal sensors. Due to its high resolution, an IR camera is able to scan large areas and detect critical points, such as hot spots. In case of failure, the camera can be replaced within a minimum of time and without having to dismount the mold.
Consistent tempering enables permanently optimized cycle times. This process also leads to an improvement in production start-up and a reduction in start-up scrap. The even temperature distribution ensures sustainable quality improvement.
Rejects due to tempering errors are detected immediately, which reduces rejection and complaint costs. One advantage inherent in statistical process monitoring is the ability to have mold servicing carried out in good time and thus prevent unscheduled repairs. And last but not least, the traceable “thermal fingerprint” (thermal image) is an important process parameter.
SKZ has licensed the worldwide usage rights for the inline thermography to Wittmann Battenfeld. The marketing and communication about this technology are handled exclusively through Wittmann Battenfeld and SKZ.
Advice on the technology and the required equipment and software purchased through Wittmann Battenfeld are designed to enable end customers to make use of the technology on their own. Besides the thermographic camera, only Wittmann Battenfeld peripherals are used in the application of the technology.
So as exclusive distributor for inline thermography, Wittmann Battenfeld offers its customers both advice and the equipment for this technology.
At the Fakuma, the inline thermography will be exhibited on a MacroPower 650. This machine will demonstrate the production of stackable transport crates. The quality of the parts will be ensured by means of inline thermography. On the exhibition unit, a Wittmann W843 linear robot will present the parts to the camera in various positions immediately after ejection. The evaluation will be displayed on a monitor along with the deviations from the release specifications and calculated segment-dependently for the Wittmann Flowcon flow regulation unit connected to it.