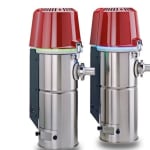
The Polish market is one of the most important European markets for plastics processing. Since the beginning of 2016, the Wittmann Group has been active in Poland with a subsidiary of its own for its entire product portfolio and is therefore presenting itself with a larger exhibition area this year. At this Plastpol, the Wittmann Group will showcase two machines from the PowerSeries as well as a wide range of robots and peripherals.
In the area of injection molding machines, the company will exhibit one machine from its all-electric EcoPower series and one from its servo-hydraulic SmartPower series. Both models offer ultimate standards in terms of energy efficiency, precision and user-friendliness. The machines equipped with the KERS (Kinetic Energy Recovery) system enable utilization of the released deceleration energy within the machine.
At the Plastpol, the functionality of the EcoPower will be demonstrated by the production of a PBT espresso cup and saucer on an EcoPower 180/750 with a single-cavity mold supplied by Hein, Austria. The parts will be removed and deposited on a conveyor belt by a Wittmann W823 robot.
The second machine on display at this year's Plastpol will be a SmartPower with 250 kN clamping force. Apart from their energy efficiency, high precision and user-friendliness, the machines from the SmartPower series stand out primarily by their compact design, high speed and cleanness. They come with an extremely energy-efficient servo-hydraulic drive as standard, which offers the additional advantages of small dimensions and a low noise level.
The SmartPower 25/130 shown at the fair is equipped with a microprocessor-controlled Flowcon plus flow controller integrated in the machine's control system. A PA ball filter is produced with a 4-cavity mold supplied by Zimmermanntechnik (HK) Ltd., Hong Kong, which has a production plant in Shenzen, China, and service subsidiaries in Germany, Austria and Mexico. The Flowcon handles closed-loop flow control and mold temperature control as well. This constitutes a substantial contribution to improvement in product quality and production stability. Moreover, thanks to the integration, the extensive parameter settings of the Flowcon are saved together with the mold data set in each case. This enables extremely comfortable and faultless operation of the appliance.
In the automation sector, a WP80 sprue picker will be on display at the Plastpol, featuring extremely low vibration in the vertical axis and high precision in parts removal, as well as W833 pro servo robots with a new B-C servo axis, a W821 UHS and a W818 designed for smaller injection molding machine models. The W833 pro is a robot equipped with the patented Wittmann telescopic stroke of the new pro series, which offers compactness, user-friendliness, extreme energy efficiency and conservation of resources, as well as a low noise level. The W821 UHS (Ultra High Speed) robot is specially designed for extremely rapid parts removal and permits mold opening times of less than 1 second.
Wittmann Battenfeld Polska will also present a wide range of peripheral equipment. This includes the gravimetric metering device Gravimax G14M, the volumetric metering device Dosimax Basic, the M7.3 control system for central material conveyance and drying systems and the individual S3 net material loader with ambiLED designed for the transport of smaller material quantities. The ambiLED features light signals in different colors to show different operating conditions. An important part of the exhibition program are the Drymax E30 and E60 dryer models and the segmented wheel dryer Drymax Aton G120-300-M. The Drymax Aton segmented wheel dryer consists of numerous chambers containing a loose filling of desiccant balls. In combination with the innovative 3-Save process, the design of this dryer not only ensures optimal energy utilization, but also a continuous drying process with a constant dew point.
Furthermore, the temperature controllers Tempro basic C140, Tempro D2/140°, Tempro primus C90 and C120 will be on display, as well as a selection of flow controllers. The program of the Wittmann Group will be rounded off with MAS 1 and MAS 3 grinders and the screenless beside-the-press granulator Junior 3.