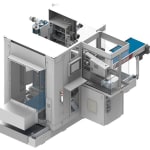
The totally revised Wittmann W837 pro IML system shown at the Fakuma stands out due to highest movement speed, modular design and optimal accessibility. In close interaction with the injection molding unit from Wittmann Battenfeld - an EcoPower Xpress 160 - the IML system demonstrates an impressive operational efficiency.
The laterally moving W837 pro robot solution reverts to many components from Wittmann's standard robot program - among these, the R8 control and the drives - thus guaranteeing the worldwide availability of spare parts. Using the R8 control, any program adjustments can be made in the same way as standard robot applications. This flexibility guarantees a future-proof investment and offers the possibility to adapt to possible future requirements.
WittmannW837 pro: compact dimensions when closed
The use of two synchronized servo drives at the horizontal axis allows for accelerations of 80 m/s², therefore enabling the shortest removal times and the shortest total cycle time. The Fakuma IML system produces injection molded lids in a 4-cavity mold at a total cycle time of less than 3.5 seconds. This is made possible through the use of 11 partly synchronized servo axes. Most of the time, these axes are on duty simultaneously, carrying out the separation of the labels, the insert of the labels, the removal of the parts, and the stacking procedure. The finished molded and decorated lids are dropped on a conveyor belt. If required, a camera inspection can also be executed. The transfer system is also used for discharging initial or bad parts that are removed from the system using another conveyor belt. Good parts are passed to a separate stacking axis. This axis especially is characterized by its stable double-sided guidance of the vertical axis, which ensures the exact positioning of the parts within the stacking area. In the case of the Fakuma show system, the product stacks are 300 mm high. The buffer line spans 2,000 mm in the direction of the machine's clamping platen, thus allowing simple subsequent handling of the finished parts.
In case of maintenance or service, the two lateral units (label magazine and stacking axis) can be moved by 500 mm each on the one-piece underframe. This ensures easy access for several components of the system.
Source: Wittmann Group