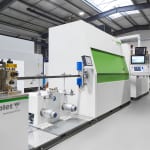
battenfeld-cincinnati and Templet are working closely together to develop systems for the production of multilayer composite pipes. In a highly competitive market, pipe manufacturers need solutions to achieve higher production speeds while maintaining consistently high pipe quality and reducing scrap rates.
Thanks to continuous new- and further developments, and the use of state-of-the-art technologies, the two partners have now succeeded in setting new standards. Machines with guaranteed production speeds of 60m/min were already delivered in 2018. Six years later, the two technology leaders have managed to develop turnkey systems that continuously produce at speeds of 80m/min. This leap in speed of 20m/min guarantees the pipe manufacturer an increase in production capacity of around 30,000 m per day.
However, it is not only the significantly higher production speeds that are worth mentioning, but also the newly designed control system. This allows the machine operators easy handling and extremely precise setting options. Various measuring devices provide the plant operator with real-time analyses that depict the production process in the form of a diagram. This enables any errors that occur to be recognized at an extremely early stage and production waste to be reduced enormously. “It is crucial that the high production speeds can be achieved continuously - simple machine operation is essential for this”, says Alexander Bonn Managing Director of Templet.
An absolute highlight of the new high-tech system is definitely the optimized control of all vacuum pumps on both, the vacuum tanks and the vacuum generators used on the coating tools. “This means that the speed of the entire system can be easily changed at any time without producing scrap”, adds Thomas Ritz, the responsible product manager at battenfeld-cincinnati. This means that the pump performance and the resulting vacuum can be assigned to the product-specific speed ramps after a one-time pre-parameterization during commissioning. When ramping the system speed up and down, this eliminates the need for manual intervention by the operating personnel, which means that saleable pipes can continue to be produced without any problems, even if the system speed is changed. “You can imagine it as follows - after starting up the production line, an operator increases the speed from e.g. 20m/min to 80m/min by simply activating the stored target ramp in the system control. The system does everything else by itself. Without any further manual intervention, the machine consistently produces flawless, saleable pipe”, adds Thomas Ritz.
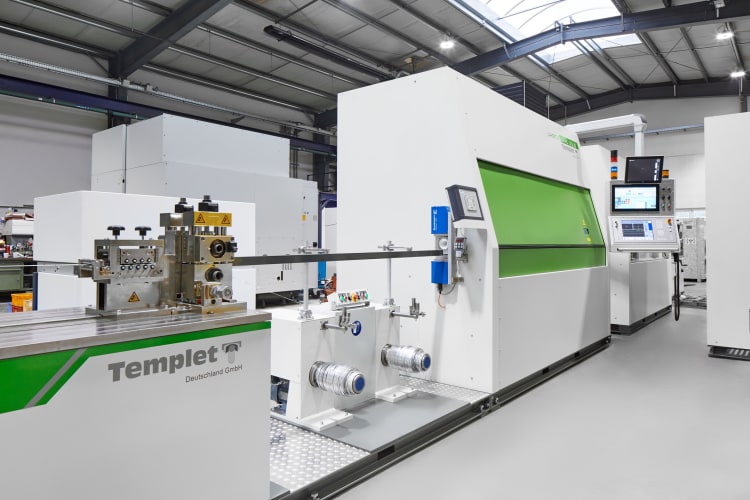
battenfeld-cincinnati and Templet offer the newly developed systems for the production of laser-welded multilayer composite pipes for a dimension range of 14-40mm. A new concept has also been developed for larger pipe diameters up to 75mm. However, it should be noted that the speeds are limited due to the larger components and the resulting lack of dynamics.
With customized solutions and their combined innovative strength, battenfeld-cincinnati and Templet Deutschland continue to achieve the highest product quality and measurable increases in the efficiency of their systems. Last but not least, customers can also count on a highly qualified, globally available service network, which guarantees high plant availability and qualified support for process engineering challenges at all times.