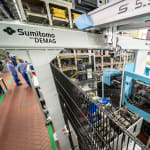
Die Entwicklung der Polymere von morgen beginnt mit dem Verständnis der chemischen und mechanischen Eigenschaften sowie des Verarbeitungsverhaltens der Materialien. Im Technikum für Spritzguss und Extrusion bei BASF in Ludwigshafen produziert eine neue vollautomatisierte Spritzgießzelle von Sumitomo (SHI) Demag mehr als 4.000 verschiedene Versuchseinstellungen pro Jahr.
Für die Entwicklung der innovativen Produktionszelle haben der Unternehmensbereich Performance Materials der BASF sowie Sumitomo (SHI) Demag in Zusammenarbeit mit H+S Automatisierungstechnik ihre Engineering-Kompetenzen und technologischen Ressourcen gebündelt. Die Fertigungszelle produziert ein breites Spektrum unterschiedlicher Prüfkörper für Produktentwicklung und Forschung aus thermoplastischen Polymeren und Compounds.
Im Mittelpunkt der Zelle steht eine hochpräzise, vollelektrische IntElect Spritzgießmaschine von Sumitomo (SHI) Demag mit 1000 kN Schließkraft. Neben den wichtigsten Entscheidungskriterien wie kompakter Bauweise, Energieeffizienz und Wiederholgenauigkeit schätzt das 30-köpfige Team im Technikum die verbesserte Komfort- und Sicherheitsausstattung, darunter der niedrige Geräuschpegel aber auch fortschrittliche, voll digitalisierte Lösungen für den automatischen Werkzeugwechsel und die Robotersteuerung.
Bei optimaler Betriebssicherheit und Effizienz erfüllt der Linear-Roboter SDR 5-35S dabei zwei Aufgaben. Zum einen sorgt der Roboter für die vollautomatische Platzierung von 12 unterschiedlichen Wechseleinsätzen aus einem Magazin in die Spritzgießmaschine. Zum anderen entnimmt derselbe Roboter mit seinem multifunktionalen Greifer den Prüfkörper aus dem Werkzeug und gibt ihn an einen kleinen Yaskawa GP8 6-Achs-Gelenkarmroboter weiter, der die Teile auf einer spindelangetriebenen Stanze ablegt, die den Anguss abtrennt.
Das vorhandene Werkzeugeinsatz-Konzept und die weitere Sonderfunktionen enthaltende Spritzeinheit wurden in die neue Fertigungszelle integriert. Erweiterungen erfuhr die Zelle durch die Einbindung der Temperiergeräte-Steuerung und die Anbindung an das neu eingeführte Manufacturing Execution System. Für Reinhard Jakobi, Leiter Verarbeitungstechnik bei BASF, ist innovativer Maschinenbau, der ausgereifte Technologie mit hochmoderner Automation und Verarbeitungspräzision kombiniert, die Basis des Erfolgs. Das Gelingen dieses wegweisenden Projekts sei dem Einsatz, der Flexibilität und der lösungsorientierten Herangehensweise des gesamten Projektteams zu verdanken.
Angelika Homes, leitende Projektingenieurin bei BASF ergänzt: „Obwohl wir mit dem Team von Sumitomo (SHI) Demag auf umfangreiche Erfahrung in der Zusammenarbeit bei der Produktion auf Standard-Spritzgussmaschinen bauen konnten, bewiesen alle Partner von Beginn an den Mut, von bestehenden Konzepten abzuweichen und Neuland zu betreten. Trotz der Komplexität des Projekts lieferten Sumitomo (SHI) Demag und H+S ein innovatives Design der Produktionszelle, das sich durch einen viel kleineren energetischen Fußabdruck und viel geringeren Platzbedarf gegenüber anderen Zellen auszeichnet.“
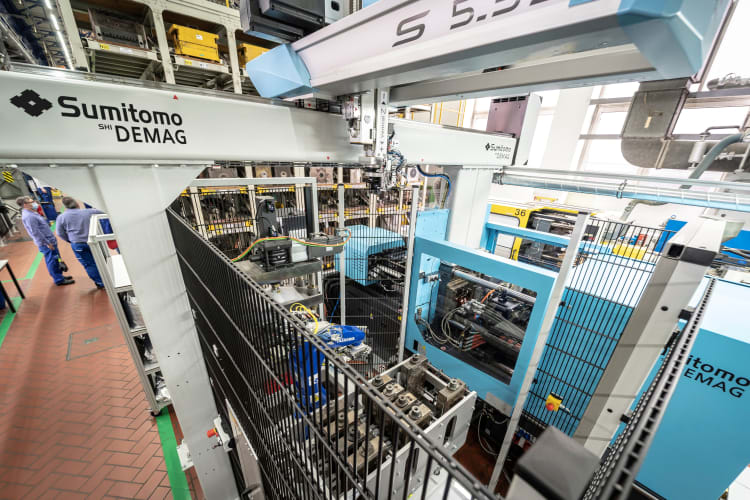
Werkzeugwechsel: immer ein heißes Eisen
Viele der Prüfkörper, die im BASF Technikum verarbeitet werden, sind glasfaserverstärkte, oft auch mit Flammschutz ausgerüstete Hochtemperatur-Thermoplaste. Infolgedessen erreichen die Schmelzetemperaturen bis zu 400°C und die Werkzeugtemperaturen bis zu 180°C.
Das Werkzeugmagazin kann über den Roboter mit 12 Wechseleinsätzen bestückt werden. Dank der Integration von HB-Therm Temperiergeräten in die Sumitomo (SHI) Demag Maschinensteuerung erfolgen die Wechsel der Einsätze in die Spritzgießmaschine auch bei hohen Werkzeugtemperaturen automatisiert und damit sicher und effizient.
Markus Hausmann, leitender Ingenieur für Automationssysteme bei Sumitomo (SHI) Demag, erklärt: „Um eine sichere Werkzeugentnahme durch den SDR-Roboter zu garantieren, wird die Temperatur auf 80°C gesenkt und der Druck im Einsatz herabgesetzt. Dafür muss unsere Maschinensteuerung nahtlos mit dem MES von BASF kommunizieren.“
Das MES der BASF benachrichtigt die Zelle, wann das Ende der aktuellen Versuchseinstellung ansteht und übergibt den Befehl zum nächsten Werkzeugwechsel an die Fertigungszelle. Unmittelbar im Anschluss an die Herstellung des letzten Probekörpers wird der Wechseleinsatz von dem integrierten Temperiergerät geregelt abgekühlt.
Als nächstes wird der Einsatzwechsel über Ausgangs- und Eingangssignale mit der Zellensteuerung synchronisiert und der neue Werkzeugdatensatz über die Roboterschnittstelle umfangtragen. Nach dem Einsatzwechsel heizen die Temperiergeräte wieder auf. Der automatische Betrieb läuft an und sobald die Werkzeugtemperatur erreicht ist, wird die Produktion einer neuen Versuchseinstellung gestartet.
Stanzen mit Präzision
Für BASF stellt die Problemlösung für die anspruchsvollen Stanzaufgaben eine herausragende Ingenieursleistung innerhalb des gesamten Projekts dar. Aufgrund des umfassenden Einsatzgebietes testet BASF ein breites Spektrum an Materialien – von weichen und zähen bis steifen und spröden Polymeren. Darüber hinaus gibt es viele unterschiedliche Probengeometrien. So variieren die Wanddicken zwischen 0,5 mm und 4 mm. Viele BASF Prüfkörper werden gemäß ISO 294 produziert. Die Norm definiert die Anforderungen an das Angusssystem und die Geometrie der Proben. „Die Formteiltrennung mittels Stanzen ist Voraussetzung, denn es verändert die Materialeigenschaften nicht und es bilden sich keine Staubpartikel“, erklärt Hausmann.
Der multifunktionale Greifer stellt sicher, dass alle Probekörpergeometrien mit höchster Präzision auf dem Stanztisch abgelegt werden. Dies ist nicht unproblematisch, da viele der Materialien, mit denen BASF arbeitet, einen hohen Glasfaseranteil haben, was Verzug bei den Probekörpern verursachen kann. Bei der Beschreibung, wie der servogetriebene Stanzgreifer die Herausforderung meistert, die Teile sicher auf der Stanzplatte abzulegen, betont Hausmann: „Werden die Prüfkörper nicht hinreichend gut fixiert, kann es passieren, dass sie schief gestanzt werden und damit nicht den spezifizierten Qualitätsstandards entsprechen.“
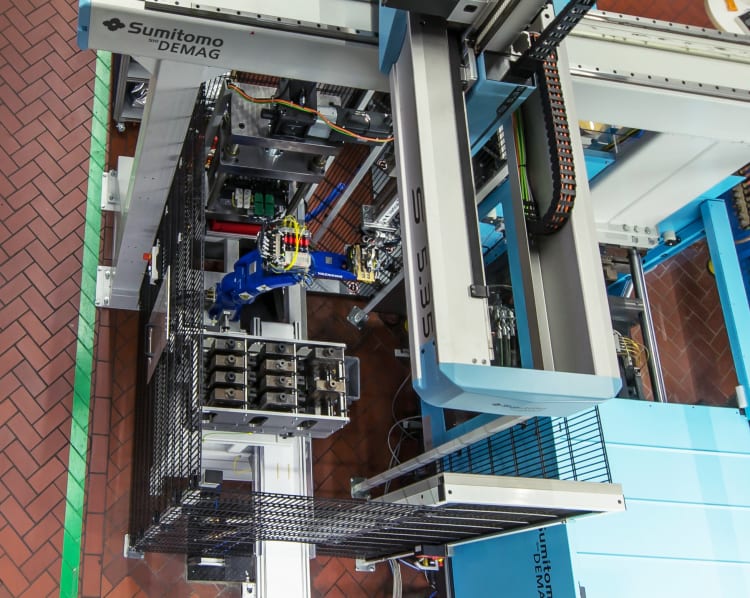
Digitale Integration
Das BASF Team fährt jeden Tag eine Vielzahl unterschiedlicher Versuchseinstellungen auf der Fertigungszelle. Dies bedeutet, dass das MES der Zelle jeweils verschiedene Material- und Prozessparameter, Prüfteilgeometrien und Temperaturen vorgibt. Jeder einzelne Spritzgusszyklus wird anschließend digital erfasst und dokumentiert.
Homes erläutert: „Das neue System zeichnet aus, dass jeder einzelne Zyklus und eine Vielzahl von Daten aufgenommen werden, was uns vertiefte Einblicke ermöglicht.“ Diese Daten sind ungemein wertvoll, da sie den kompletten Bearbeitungsablauf repräsentieren und wir tiefgreifende Rückschlüsse ziehen können, wie sich das Material unter bestimmten Bedingungen verhält und wie ein Kunde es später verarbeiten kann.“
Lösungen für die Herausforderungen unserer Zeit
Seit mehr als 80 Jahren trägt das Verarbeitungstechnikum in Ludwigshafen zum technischen Fortschritt bei und hat in dieser Zeit große Beiträge zur Lösung der Herausforderungen in der Kunststoffentwicklung und -verarbeitung geleistet. Doch ebenso wie Innovationen durch Trends vorangetrieben werden, entwickeln sich automatisierte Prozesse und die bereitgestellten Daten zum Katalysator für die Beschleunigung praxisnaher Materialentwicklungen. Die Flexibilität von Maschinen ist für diesen Erfolg ein wesentlicher Faktor, erklärt Jakobi. „Diese neue Zelle bestätigt die Bedeutung von Automation und Digitalisierung bei der Materialentwicklung sowie der Simulation und Auslegung von Bauteilen.“
Doch wie BASF erkannt hat, hängt der Erfolg ebenfalls davon ab, dass alle Partner ihr Industrie- und Engineering-Knowhow bündeln und ihre jeweilige Expertise bei den Themen Automation, Verarbeitung und Integration teilen. Indem sie dieses Wissen zusammentrugen, haben BASF, Sumitomo (SHI) Demag und H+S Automatisierung ein System entwickelt, das die Herstellung von Probekörpern und die Materialentwicklung auf ein ganz neues Level hebt.
“Für die Anstrengungen der BASF, nachhaltige Produkte und Lösungen für die Industrie zu entwickeln, ist eine solche automatisierte Spritzgießzelle unverzichtbar. Ihre Kapazität, jährlich mehr als 4.000 unterschiedliche Versuchseinstellungen für Hochleistungspolymere mit komplexen Formulierungen zu fahren und die Ergebnisse mithilfe des MES Systems digital zu verfolgen, beschleunigt diese Innovationsbemühungen“, erklärt Hausmann abschließend.