3D printing also promotes what can be called the consolidation of complexity. This is done as the technology can combine parts and features in one build that would otherwise have to be post-processed or assembled using conventional injection moulding and allied technologies, again driven by the design flexibility that 3D printing offers. Parts can be produced using 3D printing that are more ergonomic and which incorporate multiple parts and features which would be impossible or prohibitively expensive to achieve via the fabrication of highly complex tooling required for injection moulding.
3D printing requires no tooling and is agile which facilitates quick production turnaround. With 3D printing, part cost is not connected with part complexity. As soon as complexity is introduced to an injection moulded part, the requirement is for more and more expensive mould tools, which leads to an exponential increase in costs until part production is no longer viable. As 3D printing adds material, complexity of design and different incorporated shapes do not affect the amount of time that it takes to produce a part, and therefore does not lead to increased costs
Beyond non-costly part complexity, using 3D printing for production also facilitates nearly unlimited geometric freedom, exhibits very low to zero iteration costs, and has low downtime in the production cycle.
Conversely, injection moulding makes design iterations costly, and beyond the high cost of upfront tooling which as mentioned increases with increased part complexity, means that production is restricted to the location of the production tooling. 3D printing technologies manufacture direct from 3D CAD files, so the location of manufacture is much more flexible.
Also, as 3D printing is a digital process, it can be stopped post-part build or post-run and started again without punitive cost, meaning that production volumes can be exactly aligned with demand day to day, week to week, month to month. With injection moulding, once the production process is initiated, it needs to fulfill the full run immediately to remain economic, which therefore necessitates the need for warehousing which itself increases the cost per part.
3D printing is a highly reliable, cost-effective, and relatively easy-to-use production technology for short to medium volume applications and can rival injection moulding.
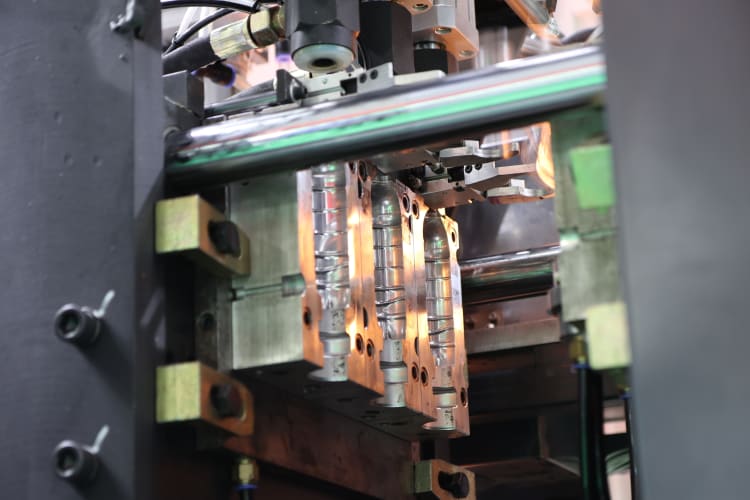
The best fit
Injection moulding finds its sweet spot in large batch production where the requirement is for the manufacture of many thousands of identical products simultaneously. It is also best suited to robust designs based on one continuous form, and the process can produce products with superior smooth surface finish without the need for post-processing (which is typically needed with 3D printing parts).
3D printing finds its sweet spot in the area of prototyping, and small to medium d production runs of geometrically complex parts and components with gaps, holes, or voids. It is also the best fit for the manufacture or parts where the design will frequently evolve or where customization is required, as design changes can be accommodated even in production.
These respective sweet spots are quite discrete and play to the fact that forward thinking manufacturers could in fact be looking at 3D printing and injection moulding as complimentary processes rather than competitive processes. When used constructively together, for example, pre-production cycles can be dramatically shortened before large volume production is undertaken.
Conclusion
It seems likely that moving forward, runs of perhaps 10,000 and below will soon be the domain of 3D printing, which for such volumes will render injection moulding if not redundant, increasingly irrelevant when looked at through the prism of cost and time of production. However, injection moulding will never be replaced, as it will typically be the technology of choice for higher volume runs.
Perhaps the biggest advantage of the use of 3D printing, however, is that although per part it is slow compared with injection moulding, its advantages in terms of design freedom, creation of geometric complexity, and part consolidation all stimulate innovation. These factors alone may be a spur to using 3D printing for multiple smaller batch runs rather than bowing purely to the economics of using injection moulding for high volume manufacture.
www.3dprint-uk.co.uk