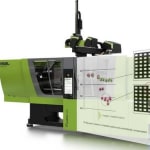
The ENGEL stand will revolve around the self-optimising injection moulding machine. The production of inject 4.0 logos will clearly demonstrate how the potential for efficiency and quality that Industry 4.0 offers can be maximised with minimal effort. For this purpose, the e-motion 80 TL machine is equipped and networked with intelligent assistance systems. The networking of production systems, the systematic use of machine, process and production data and the deployment of intelligent assistance systems is enhancing the productivity, efficiency, and quality of production operations. At the same time, processors can respond to requirements – which are changing ever more quickly – with maximum flexibility.
At the trade fair, the injection moulding machine’s CC300 control unit will simulate fluctuations in the raw material and ambient conditions. Visitors to the event will be able to watch live as the machine identifies deviations and automatically readjusts the parameters before even a single reject moulding is produced.
Compensating for fluctuations before rejects are produced
Three assistance systems from ENGEL’s iQ product range will be on show at the trade event. iQ weight control analyses the pressure profile during the injection process and compares measured values by means of a reference cycle. The injection profile, switchover point and the holding pressure profile are adjusted to the current conditions for every shot, which keeps the injected volume constant during the entire production run. At the same time, iQ clamp control calculates mould breathing in order to determine the ideal clamping force and adapt it automatically. iQ weight control compensates for process fluctuations before rejects are produced. The intelligent assistance system is available for electric and hydraulic injection moulding machines.
iQ flow control is the latest iQ assistance system that ENGEL will be unveiling to a Scandinavian audience at Elmia Polymer. By connecting the temperature control units to the injection moulding machine, the software can regulate the rotational speed of the pumps in the temperature control units on demand. The result is much lower energy consumption and the stability of the temperature control process is also enhanced. e flomo is capable of actively controlling the temperature difference in all individual circuits and automatically setting the required flow rate for each temperature control circuit.
Together with its partner HB-Therm (St. Gallen, Switzerland), ENGEL has developed a series of particularly compact temperature control units for the new integrated temperature control solution. By linking the e-temp control units to the injection moulding machine via OPC UA, the development partners have established a milestone along the road to the smart factory. The OPC UA protocol facilitates powerful, platform-independent and above all secure communication, both at shop floor level and with superordinate control systems. For this reason, it is increasingly becoming the standard for the plastics industry.
The recently developed e-temp temperature control units will be integrated into the CC300 control unit of the injection moulding machine via OPC UA.