A circular guidebook for EE&A
German materials supplier Covestro and Chinese consultancy REnato lab are jointly launching a “Circular Design Guidebook” for the electrical, electronic and household appliance (EE&A) industry. With circularity gaining importance in that sector, the firms note that more and more manufacturers are talking about their sustainability goals, in particular about an increased use of recycled materials in their end products.
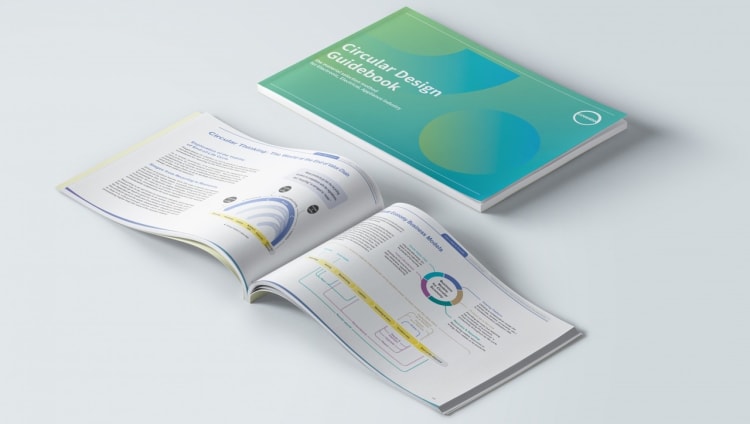
Covestro and China’s REnato lab collaborated on this Circular Design Guidebook targeting the electrical, electronic and household appliance (EE&A) sector.
"The key to solving the problem of material waste is to consider the end of product life in the initial design phase to facilitate recycling," said Lily Wang, senior vice president and global head of EE&A in Covestro's Polycarbonates segment. The book uses case studies and processes to explain material selection so that products meet sustainability and recyclability requirements. It also describes the resource constraints facing the industry, supply chain-oriented thinking, relevant business models, and provides a basic introduction to the circular economy.
From household trash to resin
Israel's UBQ Materials said March 22 that it has just earned a pair of ISO quality certifications for its “climate-positive” material derived from landfill-destined household waste. The company's patented technology converts landfill-destined household waste into a sustainable, bio-based, cost-competitive thermoplastic material called UBQ. The firm says the resulting resin can fit seamlessly into current manufacturing practices and be used to make products for a variety of sectors.
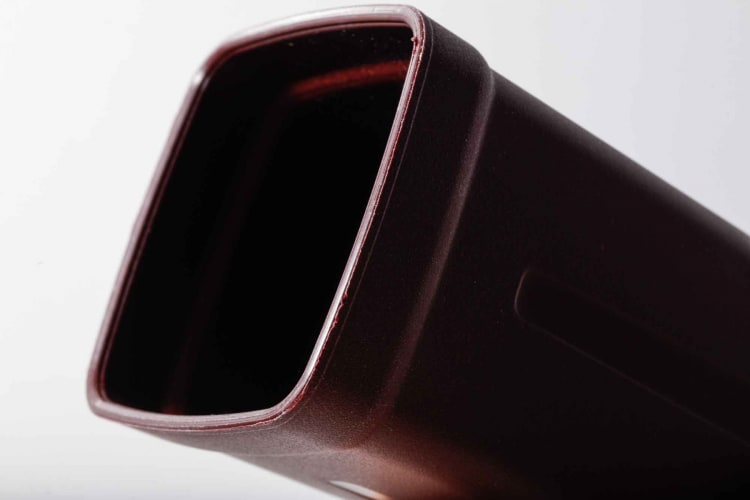
Israel’s UBQ Materials claims its material, made from municipal solid waste, is “the greenest thermoplastic material on the planet.” Here, it is shown after being molded into a trash bin.
For every ton of UBQ material produced, the company says, nearly 12 tons of CO2-equivalent emissions are averted, “preventing significant greenhouse gas emissions from landfills where municipal waste would otherwise decompose and release methane and other toxic gases into the environment.”
Enabling 100% PCR packaging
Avient Corp. has launched a new masterbatch made with post-consumer recycled (PCR) polyolefin as a carrier resin that “aims to make production with 100% PCR an industrial reality.” The product, called Rejoin PCR Masterbatch, can enable a bottle or part to be manufactured entirely from PCR, the Ohio-based company said.
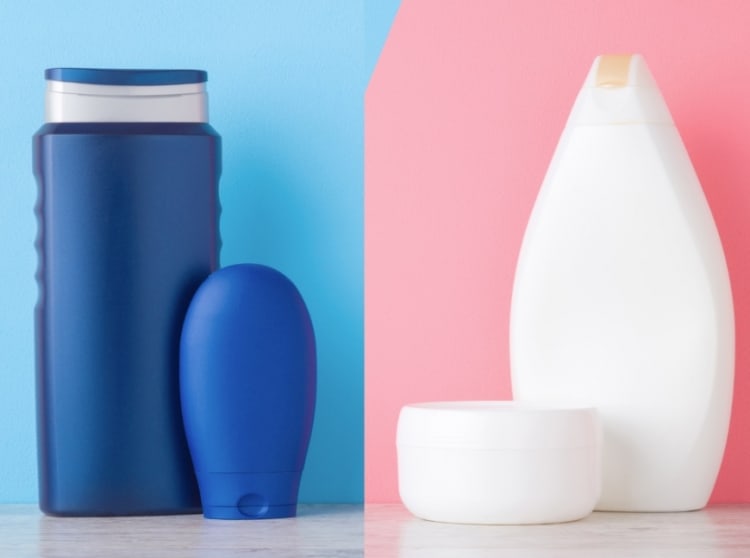
Avient says its new masterbatch made with post-consumer recycled polyolefin as a carrier resin will make production of bottles such as these with 100% PCR a reality.
Until now, it noted, masterbatch generally has been made using virgin material as a carrier resin. This means that at typical let-down ratios, the finished product would contain 3% to 5% non-recycled plastic. This development will help major consumer goods companies to meet their sustainability goals of 100% PCR polyolefin packaging, according to Bob Lee, Avient’s marketing director, Color & Additives Asia.
Many different eco-options
There are numerous ways to strive for circularity, and it’s clear that no single approach alone can achieve the ambitious aims laid out by the Ellen MacArthur Foundation and others focused on eliminating plastics waste.
But EMF remains optimistic, stating: “Our economy is currently locked into a system that favors the linear model of production and consumption. However, this lock-in is weakening under the pressure of several powerful disruptive trends. We must take advantage of this favorable alignment of economic, technological, and social factors in order to accelerate the transition to a circular economy.
“Circularity,” the nonprofit group says, “is making inroads into the linear economy and has moved beyond the proof of concept; the challenge we face now is to mainstream the circular economy, and bring it to scale.”