The measured values from various sensors can be visualised in the machine control system and individual events, such as warnings, alerts and error messages, can be displayed and documented. This allows users to identify anomalies in the process quickly and assess what needs to be done.
Setscrews for greater efficiency and reduced costs
To significantly simplify everyday injection moulding using digital products and services, Arburg has developed the arburgXworld customer portal with its many apps, the basic versions of which are even free of charge. On top of this, there are the company's own Selogica and Gestica control systems, including the associated assistance and pilot functions, which visitors can find out more about at Fakuma using a Gestica demonstration model. The control system is the "intelligent" head of the machine and can provide operators with comprehensive and active support during set-up, setup and operation - which quickly pays off in times when skilled labour is in short supply and personnel costs are high. Digital features can be used to unlock significant optimisation potential in injection moulding machines with regard to production and cost efficiency.
- The premium "MachineFinder" app helps users find the most suitable machine from the inventory and immediately provides the corresponding recommended values for initial calculations.
- To keep set-up times short, the "Set-up Assistant" supports operators step by step – from menu-guided mould installation and automatic initial calculation of parameters to teaching in the sequence.
- The "Virtual Control" app provides previews of the sequence programming and can optimise data sets directly on the PC.
- With the help of an AI-supported variant analysis, the injection moulding simulation is automated with the "FillAssist" assistance function and "learns" the effects of changes to machine parameters. The filling simulation integrated into the control system is designed to quickly reach the good part and enter a stable production phase on start-up.
- "EnergyAssist" automatically heats up or deactivates the cylinder module and mould in a consistent and controlled manner, thereby significantly reducing the energy requirement and costs.
- "CycleAssist", which enables the control system to know the programmed cycle, reduces part costs for customers by optimising cycle times. Unproductive times can be eliminated and the cycle time optimised at the click of a button. At Fakuma 2024, this will be demonstrated in a packaging application, for example, with an electric Allrounder 520 A.
- In turn, "Meltassist" automatically calculates the plasticising capacity utilisation and residence times and actively helps to save material.
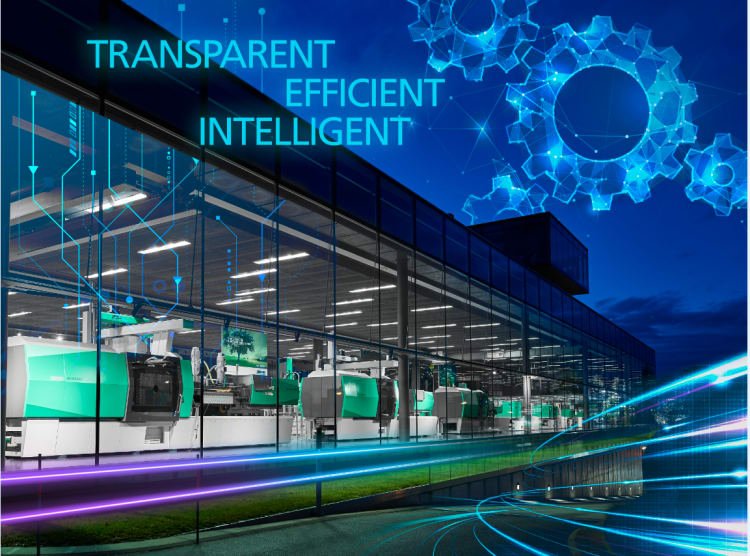
Improving part quality
One challenge in terms of part quality is the processing of alternative and demanding plastics, particularly post-industrial recyclates (PIR) and post-consumer recyclates (PCR). Even with batch changes or non-homogeneous virgin material, pilot functions in the Gestica control system can ensure stable processes.
- "aXw Control RecyclatePilot" utilises the existing machine sensor systems to reliably even out fluctuating material qualities and keep the shot weight constant. This significantly reduces the reject rate.
- Errors in the filling process can be compensated for with "ScrewPilot" to ensure stable mould filling, while
- "PressurePilot" provides bionically optimised pressure regulation to avoid underfilling or burr formation. Both pilot functions are active in the production of medical syringe plungers with a hybrid Allrounder 570 H.
- "ReferencePilot" enables precise holding pressure regulation with the aid of cavity pressure sensors.