The data from the injection moulding process as well as data relevant to quality and service can also be made available to higher-level software tools and platforms. With the Arburg Turnkey Control Module (ATCM) Scada system, process and quality data can be combined on a part-specific basis and important system functions can be visualised. To achieve this, the injection moulding machine, automation systems and peripheral equipment each send all relevant data to the ATCM. This makes every single moulded part 100 per cent traceable. At Fakuma 2024, a vertical Allrounder 375 V producing vacuum housings will be on show. The part-specific data from the injection moulding process and automation are linked to the results of the visual inspection of the insert. The fully automated application is also an application example of the R-Cycle initiative, in which digital product passports are used to record relevant recycling data in real time during the product life cycle and create the foundation for data-based material flows.
Increasing planning efficiency and creating transparency
IT-networked injection moulding production requires machines to be connected to a manufacturing execution system (MES). The Arburg host computer system ALS is a central MES that can be used to digitally plan, optimally utilise and effectively control the entire production process and track all relevant information.
As early as the planning phase, an assistant can make suggestions for a best-fit machine based on collected production data and user-dependent criteria thanks to an intelligent algorithm. All the information on orders, production progress, set-up times and maintenance is available centrally. The associated data sets can be transferred to the injection moulding machine in a fully automatic process. With the trend towards paperless production, the number of linked production documents is also increasing. Relevant documents are provided for the respective order, regardless of location or media.
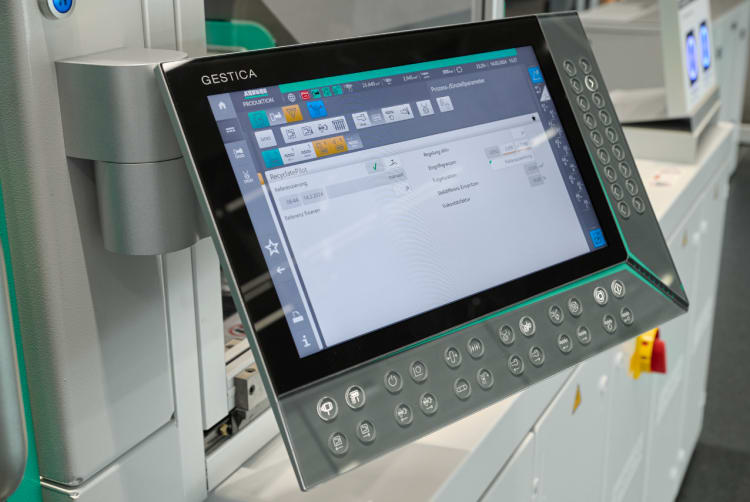
One major advantage is that production data can be recorded and analysed in real time. Key performance indicators (KPIs), key figures and production reports help management make the right decisions and adapt to changing conditions with agility. For continuous quality assurance, it is possible to carry out statistical process monitoring (SPC) and evaluate the process parameters of the injection moulding machines in real time, regardless of location.
All in all, ALS ensures greater flexibility, efficiency and transparency in production. On average, overall equipment effectiveness (OEE) and overall plant efficiency can be significantly increased by around 26 per cent with ALS. Linking to the arburgXworld customer portal opens up even more possibilities. ALS and the customer portal are also available as mobile versions for smartphones and tablets. A new and groundbreaking feature is the AI-supported "Ask Arburg" app, for example, which contains easily accessible, comprehensive injection moulding knowledge from Arburg and can answer specific questions about all Arburg products and processes relating to injection moulding.
Summary and outlook
Arburg's comprehensive expertise is embedded in its digital services and products. They are powerful tools that contribute significantly to the future-proofing and resilience of a plastics processing company. They can be used to optimise production sequences, record data in real time and improve and document the quality of moulded parts. This means that getting started with digitalisation is very easy and flexible and pays for itself quickly. Complex production environments and high-precision components in particular require precise process control, and this is where the host computer system, in conjunction with the arburgXworld customer portal, can achieve significant benefits in terms of transparency, process reliability and energy and production efficiency.
As the number one in the industry when it comes to digital transformation, Arburg is also working intensively in the field of artificial intelligence. The aim is for AI-based systems to learn correlations themselves and actively readjust processes in order to optimise the yield and quality of injection moulded parts in series production. Arburg's vision is that, with the help of AI, every injection moulding machine in the future will not only know the processes, but also the products it produces.