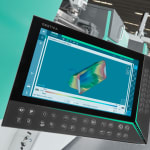
From small contract injection moulding companies to large global players, plastics processors are all facing similar challenges in the current difficult economic environment: they need to react flexibly to market changes and increasing cost pressure if they want to produce products competitively and profitably. Digitalising injection moulding processes can achieve significant benefits here if implemented correctly. Arburg has been dealing with this topic for decades and is on hand with advice and support to help its customers find the "smartest" solution in each case. Digital technologies can be used to produce plastic parts with maximum efficiency, flexibility, transparency and impeccable quality, as Arburg will be demonstrating live in ArburgSolutionWorld and with numerous exhibits at Fakuma 2024.
Arburg has extensive expertise and a wide range of products and services for implementing customised digital solutions - from control systems and associated assistants developed and manufactured in-house to the company's own host computer and Scada system and the customer portal
The individual solution modules, correctly combined depending on the requirements and environment, provide the answer to what is probably the most important question for Arburg customers in connection with digitalisation: how do I get the data that is relevant to me and how can I use it to make my processes even better, more efficient and more competitive? The key here is that it is not the sheer quantity of data collected, but its quality and relevance that form the basis for successful process optimisation. Artificial intelligence (AI) opens up completely new prospects and possibilities when it comes to processing large amounts of data and drawing meaningful conclusions from it. For example, the relevant data can be used to create forecasts for maintenance requirements (predictive maintenance), generate paperless evaluations and documentation in real time and access injection moulding knowledge with the help of AI-supported apps. In this way, sequences can be dynamically controlled and optimised in "smart" production, allowing available resources to be used even more efficiently - for example in order planning, quality assurance, mould management and maintenance.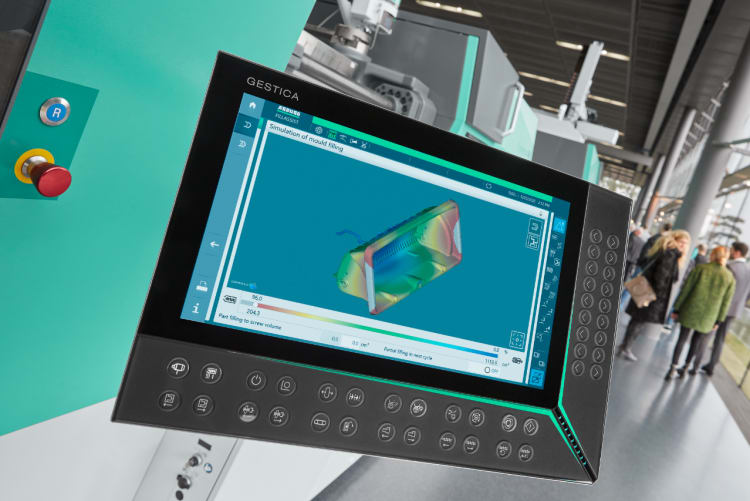
Communication in a standardised language
As a rule, temperature control units, robotic systems and other pieces of peripheral equipment are also integrated into the injection moulding process. The aim is for all the components to interact as simply and reliably as possible - ideally from a central control system and on the basis of synchronised values and parameters. To achieve this, data must be exchanged "in one language". The OPC UA interface, which is not tied to a specific manufacturer, is the ideal solution for this. At Fakuma 2024, for example, the LSR dosing unit will be communicating with the Gestica control system via Euromap 82.3 during the production of multi-component spatulas with an Allrounder More 2000. Communication takes place via standard Ethernet and standardised plug connectors. Devices are automatically recognised and integrated into the control system using plug and play. For standardised interlinking, all Arburg injection moulding machines are equipped with an IIoT gateway as standard and have basic connectivity.
Ideally, the "smart" machine is comprehensively interlinked, monitors its processes, controls them adaptively and actively supports operators in intuitively setting up production sequences. Using "smart" services, operators can receive quick and targeted explanations, picture-by-picture instructions and error analyses as required via remote access or an app. If any unscheduled standstills do occur, spare parts can be ordered online around the clock via an interactive catalogue.
Predictive maintenance ensures that things don't get that far. This requires "smart" communication between the machine or production cell and its centrepiece, the injection mould. At Fakuma 2024, an Allrounder 720 E Golden Electric will be equipped with a 24-cavity mould from Hack together with "Moldlife Sense", a computer system that enables sensor-controlled mould monitoring over a mould's complete life cycle, for example, and detects changes to the mould at an early stage.