Online support, remote service, augmented reality - the functions are now already widely used. What are your achievements in this area?
We see ourselves not only as a machine supplier, but rather as a technology partner, efficiency driver, and pioneer in the plastics industry when it comes to digitalisation. Our machines, automation and proprietary IT solutions form a flexible production system. The ultimate goal is to make the complex controllable. We equip our Allrounders with an IIoT gateway so that they can be interlinked in a standardised way with the arburgXworld customer portal or the Arburg Remote Service, for example.
We have combined our digital products and services intelligently and clearly in the arburgXworld tool. With our customer portal of the same name and its many apps, we map the entire world of our customer's company, so to speak, and make it easier to get started in Arburg's digital world - across the entire injection moulding value chain. The portal offers real added value and many features to make everyday work even more efficient – all available in a basic version that is totally free of charge and therefore also risk-free. The Shop and MachineCenter are particularly in demand. In the Shop, customers can very conveniently order spare parts at any time and at attractive conditions. With its central access to production-relevant information and documents, the MachineCenter offers transparency about the company's own machine fleet and simplifies planning. The VirtualControl function, on the other hand, is the digital control twin, so to speak. The machine setter can use a PC or tablet to create and change injection moulding programmes from home, optimise sequences, and carry out troubleshooting - even across locations. Data can subsequently be transferred directly to the machine via the ARBURG host computer system (ALS), for example, or on a compact flash card.
The SelfService app is another modern tool. This is where the service technicians' knowledge database is stored. In the event of a machine fault, there are instructions for self-help - which avoids time-consuming and costly on-site service visits. In future, the Gestica control system will also provide 'first aid' by using 3D animations to show the operator exactly where the malfunction is located and then assisting with troubleshooting via the operating instructions.
Many customers are avoiding business trips and site visits due to the coronavirus pandemic. For this reason, we now also offer the option of remote machine acceptance. During the process, our sales experts go through the requirements specification together with the customer. On completion, they receive a detailed report including additional documentation in the form of images. The approach saves time and money and is an exciting option for the future. Just like our online support via the Arburg Remote Service, or 'ARS'. This allows hotline staff to connect directly to the machine's control system via a protected and encrypted data connection. The machine operator actively enables VPN access via software switch. This secure online support enables customers to quickly and easily use the extensive skills of our service experts to analyse as well as optimise their processes.
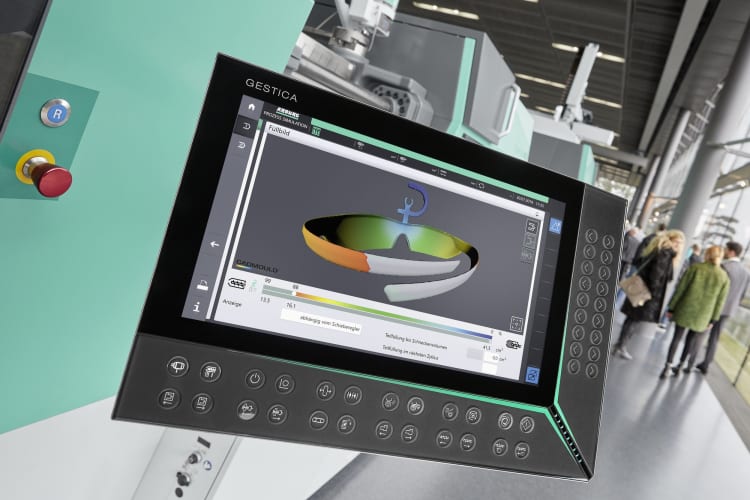
aXw Control FillAssist - tool for setting up a mould to speed up the process and make it more reliable at the same time