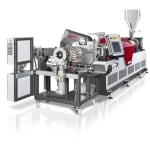
Large Surface Area – Low Vacuum
When processing PET on an extruder, moisture must be removed from the material in order to avoid hydrolysis, leading to breaking down of the polymer chains and reducing the material’s viscosity. Conventionally, the material is dried before processing on the extruder. The material is dried in large containers for up to 8 hours and at temperatures of around 160°C. When dealing with recycled PET, especially PET bottle flakes, the moisture content can be 1% or even higher. The pre-drying for the most part determines the IV of the end product. The melt viscosity can be monitored with an online viscometer, but the extrusion process cannot be controlled to significantly influence the IV of the end product (unless IV enhancing additives are used).Several so called "dryer-less" extrusion technologies offer an alternative to pre-drying. One of these technologies is the MRS Extrusion Technology from Gneuss. This design processes the PET so that the chemical equilibrium reaction of hydrolysis is influenced toward long chain molecules by extracting moisture in the melt phase, thereby ensuring the necessary viscosity. With the MRS Extruder, amorphous PET pellets or recycled material can be processed without pre-drying. This is possible, because in the extruder, the polymer surface is exchanged at an extremely high rate under vacuum. The constant and rapid surface area renewal rate ensures efficient removal of moisture and other volatiles.
The basic design of the MRS Extruder is that of the single screw, however with a special degassing section. In this area, the polymer enters a special drum which rotates with the main screw. This drum contains eight small, open extruder barrels in the longitudinal axis, which contain satellite screws. These screws are driven by a ring gear and rotate around the main screw and in the opposite direction. This disproportionally affects the surface area exchange rate of the polymer. The barrels in the rotary drum are approximately 30% open so that optimum exposure of the polymer is achieved.
The large and constantly renewed polymer surface which is some 25 times greater than that of a vented counter rotating twin screw extruder, enables unmatched devolatilising performance at a relatively moderate vacuum. In contrast to other dryerless technologies, it is not necessary to pull a deep vacuum. A vacuum of between 25 and 40 mbar is adequate, even with an input material residual moisture level of 1% (10.000 ppm). This makes the vacuum depth an additional parameter that can be adjusted to e.g. achieve a certain melt viscosity. In fact, the extraction of volatiles is so effective, that this extruder type has unrestricted FDA approval so that PET bottle flake can be processed to food contact products.