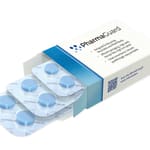
With PharmaGuard, a PP-based, recyclable blister packaging solution, Südpack Medica paved the way for greater sustainability in the pharmaceutical industry. But that was just the beginning. The film manufacturer is already developing the next generations of its future-proof packaging systems that combine sustainability with exceptional quality and reliability. Through its development partnership with IMA, Südpack is working to ensure that these new mono-material structures can be processed on customers’ existing blister lines with the same efficiency, product protection, and packaging reliability as conventional PVC/PVDC solutions.
While current regulations do not yet require recyclable packaging or recycled content in the pharmaceutical sector - as they do in the food industry - pharmaceutical companies would be well advised to start preparing for future packaging requirements now. To make the transition to sustainable blister packaging as easy as possible for customers, Südpack and IMA are actively developing market-ready solutions. Their goal is to ensure that the new materials can be seamlessly integrated into customers’ existing machinery.
The development of PharmaGuard was undoubtedly a milestone in pharmaceutical packaging. This innovative packaging concept sets new standards in terms of sustainability, quality, and performance. However, maintaining this high level of performance presents a real challenge, as PP- and PE-based mono-materials introduce entirely new requirements for the packaging process.
At Südpack, polypropylene (PP) is the preferred polymer ...
… for oral solid dosage packaging. PP-based structures, such as PharmaGuard, stand out due to their intrinsic water vapor barrier, low specific weight, high transparency, and excellent push-through performance. This material is free from phthalates, nitrosamines, PFAS, and halogens and meets the strict requirements of USP 661 and the International Pharmaco-poeia. Most importantly, unlike conventional PVC/PVdC blister solutions, PP-based packaging concepts can be integrated into existing recycling streams. A Sphera LCA study, commissioned by Südpack and verified in accordance with ISO 14040/44, has confirmed that PP has a smaller carbon footprint compared to traditional composite materials such as PVC/PVdC and aluminum, as well as PET-based mono- and multilayer materials.
A relentless focus on customer requirements
What may seem like a seamless solution is actually the result of years of development by the pioneering film manufacturer. However, to ensure that the new high-performance films run smoothly on customers’ existing blister lines, the machine manufacturer’s expertise is also indispensable. The primary goal of this partnership is to minimize the time, effort, and costs associated with retrofitting existing machines, while ensuring the same level of quality, speed, and efficiency as conventional films in the packaging process. As a result of their close collaboration during the development process, both partners - and most importantly, their customers - can now benefit from greater opportunities to analyze and optimize material performance for blister packaging applications.
To better define future-proof, sustainable packaging solutions and foster closer cooperation with material suppliers and customers, IMA has established a network of analytical laboratories through its OpenLab initiative. For example, during the development of PharmaGuard, IMA’s extensive expertise in thermoforming, sealing layer design, and printing helped elevate the material’s performance beyond that of conventional PP films.
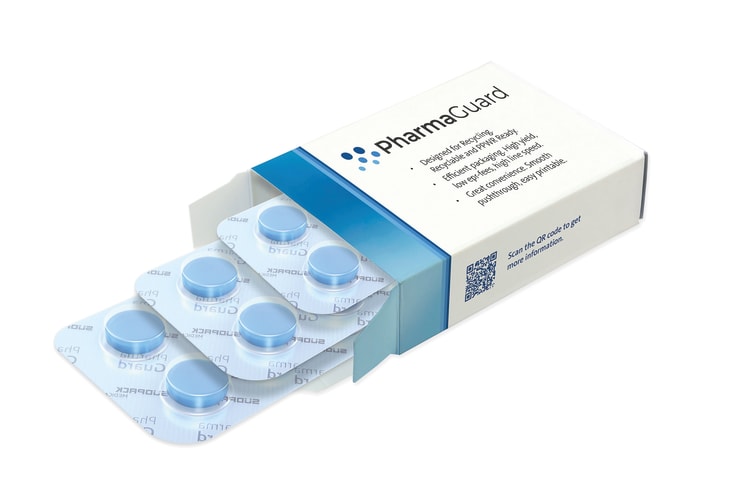
The OpenLab: data-driven analysis
The OpenLAB plays a key role in helping customers gain a comprehensive understanding of how materials behave on IMA machines. It also helps identify key factors that ensure consistent, high-quality results, including optical properties and process stability.
One of its most valuable assets is a detailed database of material structures, correlated with test results across different systems. Additionally, the OpenLab allows a dual approach to troubleshooting - any issues encoun-tered during testing are analyzed in-house from both a machine and material perspective, allowing for precise adjustments and solutions. Moreover, the lab helps identify market trends for various IMA applications by evaluating new sustainable materials.
Ultimately, thanks to data-driven insights, Südpack and IMA can ensure that the recyclability and performance of mono-materials meet both market demands and internal packaging standards. This makes it easier for customers to transition to more sustainable packaging concepts.