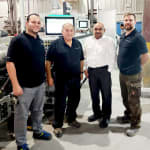
The extrusion unit with direct dosing for the production of highly filled 3-layer PVC pipes is running: "Bahrain Pipes, one of the largest pipe manufacturers in the Middle East, was the first customer to choose our modern and sustainable machine solution", Gernot Dorn, international Sales Director at battenfeld-cincinnati in Vienna, is pleased. The key feature of the combination of parallel twin-screw extruder twinEX and co-extruder conEX is the permanently installed gravimetric dosing unit on the twinEX. It allows the direct processing of chalk - without premixing. This saves energy, minimizes wear, ensures reliable dosing and provides flexibility in the use of materials.
Bahrain Pipes manufactures pipes and system solutions for various applications. These include pipes for hot water, cold water and gas supply, pipes for sewage systems and pipes for data transport systems made of PE, PP-R and PVC. More than 20 extrusion lines are in operation at the production site in Manama, Bahrain, for the production of small and large pipes, coiled pipes and corrugated pipes. A large injection molding machine park completes the extruded pipes with its own fittings to create complete systems if required. The company, which was founded in 1996, therefore has enormous expertise and a broad portfolio and has a good reputation not only nationally but also internationally. Bahrain Pipes selected the innovative extruder solution with dosing station from its long-standing machine supplier battenfeld-cincinnati primarily because of the material cost savings combined with increased flexibility. "The customer has upgraded an existing pipe line with our extruder combination and is now able to produce 3-layer pipes with a highly filled middle layer," explains Gernot Dorn.
High filler contents are of great interest for the production of PVC pipes, as the material costs still make up the lion's share of the production costs. Chalk contents of up to 65 parts (ppH) are quite common. However, the high contents do not make the production and dosing of the typically used premixes very easy. On the one hand, the high chalk content leads to increased machine wear due to its abrasiveness, both in the heating/cooling mixer and in the conveying lines, and on the other hand it can lead to demixing before being fed into the extruder, which in turn leads to reduced material homogeneity. These disadvantages are a thing of the past with the new dosing unit. Pipe manufacturers such as Bahrain Pipes can now use premixes with a low chalk content and feed the remaining quantity directly into the extruder. On the one hand, the standardized premix reduces wear in the heating/cooling mixer and, on the other hand, allows higher overall outputs, as high chalk content enables longer mixing times and smaller quantities due to its large surface area. At the same time, the standard mix in combination with the dosing unit enables product-specific recipes to be configured on demand directly on the extruder. To ensure a smooth process, the dosing unit is equipped with a closed chamber in which the chalk is kept in constant motion to prevent bridging and to guarantee dust-free operation. It is fed directly into the main extruder, the twinEX 93-34R. This is equipped with a specially adapted and wear-resistant screw geometry and ensures perfect homogenization of the middle layer. The conical conEX NG 54 twin-screw extruder ensures shiny and absolutely smooth inner and outer layers for the up to 250 mm wastewater pipes produced in Bahrain. To the customer's complete satisfaction, the line has recently been running at an output rate of 750 kg/h.
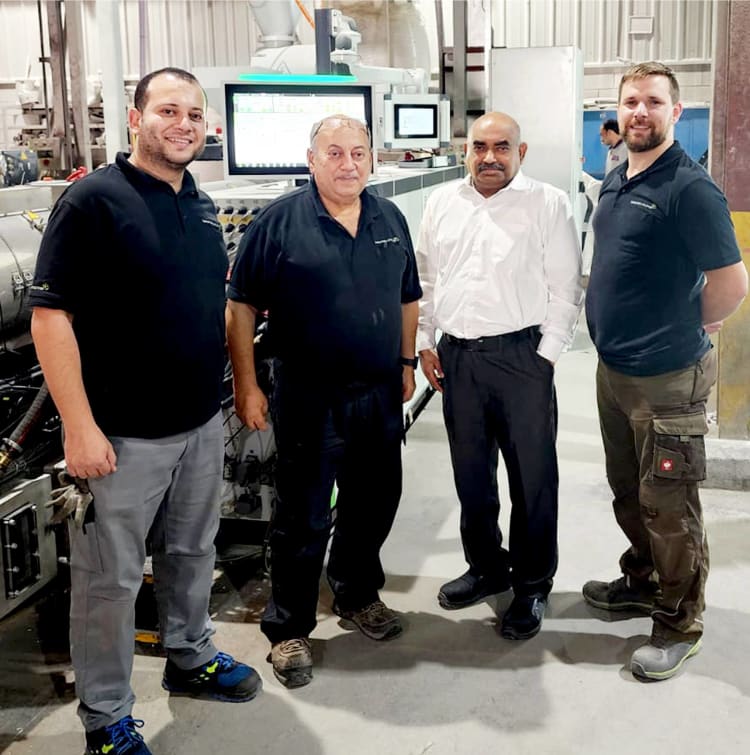