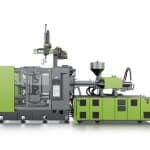
iQ solutions raising process stability and quality
Producing parts of consistently high quality shot for shot calls for more than just an accurate injection moulding machine: fluctuations in environmental conditions as well as raw materials and wear have an impact, and may necessitate the readjustment of parameters. At Plastpol, Engel will be presenting iQ weight control, software that recognises and automatically compensates for deviations from the specified melt flow by adjusting the switchover point, injection speed profile and holding pressure in the same shot. The production of complex, three-dimensional housing components using an all-electric Engel e-motion 170/110 T injection moulding machine will impressively showcase the strong potential of the software. The component design includes various breaks, delicate grid structures and alternating wall thicknesses; in this case, even the smallest changes in general conditions can mean the cavity is not completely filled and rejects are produced. "With iQ weight control, we are improving the cost-effectiveness of injection moulding production significantly," points out Piotr Nachilo, managing director at Engel Polska with headquarters in Warsaw. "Demand is increasing for self-adapting assistance systems. Integrating additional intelligence in the CC300 control unit for injection moulding machines enables customers to improve process stability and product quality, regardless of how qualified their employees may be."While the iQ weight control software optimises the injection process, the focus in developing iQ clamp control was on the injection moulding machine's clamping unit. This software will also be installed on the Engel e-motion injection moulding machine at the Plastpol event. On the machine display, visitors to the trade fair will be able to see how iQ clamp control determines and automatically adjusts the ideal clamping force shot by shot on the basis of the mould breathing.