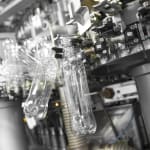
When Bernd-Thomas Kempa, who has been in charge of Sales & Service since 2012 and is now head of Plasmax Barrier Technology Global Account Management, and Dr. Joachim Konrad, who has been responsible for engineering as director of Plasmax Barrier Technology since 2014 and is now head of the Large Machine Product Division at KHS, talk about the history of FreshSafe PET, frequent mention is made of the words “persistence”, “conviction” and “trust”. Together with their team, in a manner of speaking the two are the trailblazers behind the transformation of KHS Plasmax barrier coating technology from a niche product to a market-proven, tried-and-tested packaging system for the food and beverage industries.
The story of FreshSafe PET, also known as Plasmax, began in the 2000s. This was when Schott AG and SIG Corpoplast launched a joint venture for the plasma coating of PET bottles to cater for changing packaging preferences in the industry. In doing so they pooled the expertise of an international manufacturer of glass and glass ceramics with that of a packaging producer and engineering company for the processing of plastics. Schott AG’s portfolio also included a glass coating which was applied to the insides of glass containers as a supplemental layer. “This protected highly sensitive pharmaceutical products from substance migration,” explains Kempa.
Challenges for customers and KHS
During the course of the joint venture a prototype of the first generation of Plasmax machines was developed and in 2002 the first Plasmax machine was tested in Switzerland with an output of 10,000 bottles per hour. Plasmax was also granted regulatory approval for use in the food industry in Europe, the USA and Japan. Two Plasmax 12D machines were then shipped to Japan for the protective packaging of sensitive, top-quality products. In 2006 Eckes-Granini was the first European fruit juice company to go to market using this technology. “The constant aim of development was and still is to integrate just one machine which satisfies bottling plant conditions and meets customer expectations,” says Kempa. System availability in particular had to be at an established level typical of the industry from the very start. “Looking at our success now and at the growing demand for this machine, we can say that it was worth it. We still nurture a certain start-up mentality in the team, though,” adds Konrad.
“With the dissolution of the joint venture and the takeover of Plasmax technology by KHS in 2008 we were given plenty of backing. However, as part of a global enterprise our small team was also required to prove that this technology could be just as sustainable in the beverage industry environment,” Kempa states. “Without the support of KHS and our parent company Salzgitter AG it wouldn’t have been possible to successfully transform this technology and break even. Success would have been equally lacking had we not had the special way of working together we still foster, with plenty of team spirit and great willingness shown by all members of the team,” he adds.
This support and sense of trust also increased among the company’s customers: alongside other machine sales in 2010 the prototype of the larger second generation of Plasmax coating machines went to Eckes with a capacity of up to 27,500 1.0-liter bottles an hour. In 2014 the company procured the world’s first FreshSafe block for its plant in Fallingbostel, a system blocked with a KHS stretch blow molder which produces a maximum of 32,000 0.75-liter bottles every 60 minutes. “KHS enjoys a trusting partnership with Eckes-Granini which goes back several decades where systems can be implemented to the benefit of both parties. This enabled Eckes to recognize the potential offered by a more sophisticated style of PET packaging very early on, for example, giving them optimum protection for their sensitive beverages,” says Kempa.