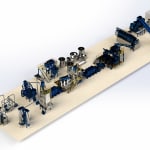
Herbold Meckesheim is reporting an excellent order situation for PET and film washing lines towards the end of the current fiscal year. Towards the end of the US fiscal year, because since last summer Herbold belongs to the US group Hillenbrand Inc. Last October, a separate Recycling Business Unit was set up under the umbrella of Hillenbrand with the machinery building company Coperion to cover the entire process chain of plastics processing. This gives the Meckesheim-based plant manufacturer an even stronger basis and more impetus for its steady growth.
The Recycling Business Unit offers comprehensive and innovative overall solutions based on the complementary and aligned technologies of Herbold and Coperion. From mechanical processing – reduction, washing, separating, drying and agglomeration of plastics – to bulk material handling, feeding and extrusion, as well as compounding and pelletizing, the Business Unit covers the entire process and thus value chain. A global network of engineering sites, project management and service centers ensures fast order fulfillment, whether in the USA or Asia, and, thanks to literally short distances, enables installation and commissioning as well as competent and fast on-site service. State-of-the-art test centers for product development and customer trials round off the Recycling Unit's range of services.
In the course of the integration, the management of Herbold Meckesheim was also restructured: In addition to Massimo Serapioni, who is also General Manager of the Business Unit, Christian Raiser took over the management of the operating business as Managing Director in July of this year. He is responsible for the success of the site and reports directly to Markus Parzer, President Polymer Division of Coperion.
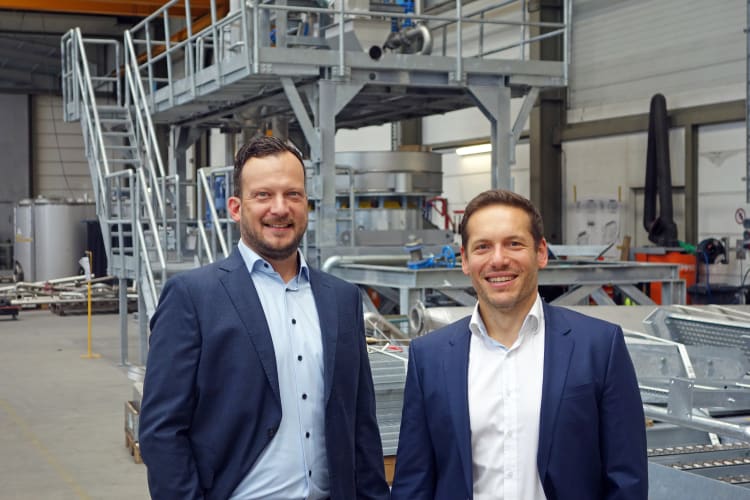
The new management of Herbold Meckesheim: Managing Director Christian Raiser (left) and Massimo Serapioni, also General Manager of the Recycling Business Unit.
Christian Raiser has learned the management of a mechanical engineering company from scratch: His professional career began in 2007 in production at Coperion in Stuttgart in the screw element manufacturing segment. From 2013, he was responsible for assembly and logistics in the former Compounding and Extrusion Division. In 2019, Raiser moved to Coperion's Wytheville site in the U.S. state of Virginia, home of parts manufacturing and assembly of ZSK extruders for the American market, as General Manager and Vice President Operations.
Not only in the United States, where Herbold has a subsidiary, but especially here the interest in the modular and automated recycling solutions from Meckesheim is unabated. And PET washing lines continue to dominate the order intake alongside those for films. There is also strong demand for lines for big bags and hard plastics in general. In addition, the special machinery manufacturer is not forgetting those customers who are still interested in single machine solutions. These are mainly granulators and fine mills as well as plastcompactors. Moreover, Herbold Meckesheim traditionally thinks of the circular economy also in terms of its own machines and maintains an extensive program for overhauling, retrofitting and selling used units.
A glance at the order books shows that it is constantly higher throughputs that are being sought by customers all over the world. In addition to the United States or the United Kingdom, the EU countries from Scandinavia to Bulgaria or Turkey and India are strongly expanding markets. Often, the inquiries here are now aimed at several parallel plant lines. The necessary mechanical processing of post-consumer material for subsequent chemical recycling on an industrial scale is becoming increasingly important too. Here, Herbold also offers its own solutions for turnkey systems together with Coperion.
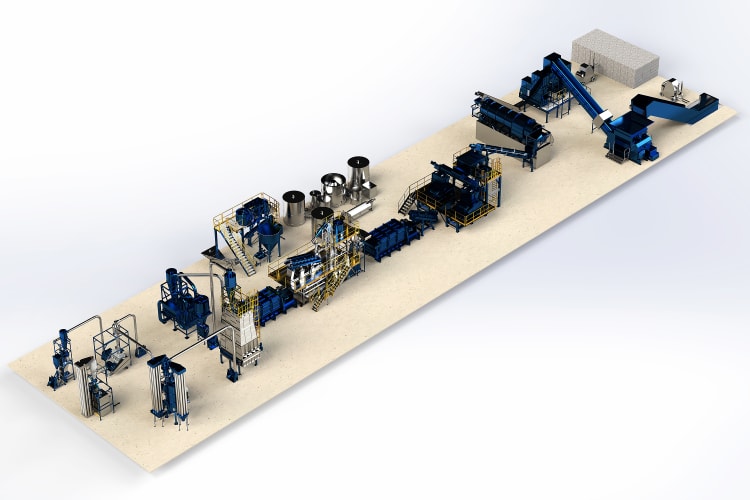
Full order books: increasingly higher throughputs of the washing lines are requested from Herbold Meckesheim by customers all over the world.
The Meckesheim-based company meets the growing customer requirements through technical advancements in machine and plant design to increase throughput, durability, wear protection and ease of maintenance as well as the purity of the recyclates on the one hand. On the other hand, energy consumption, water usage and personnel requirements are to be reduced as far as possible through efficiency and automation.
It is also clear that ever larger recycling lines are driving the demand for production space and manpower at Herbold Meckesheim. Currently, 16,000 square meters are available, distributed among logistics, assembly and technical center. Accordingly, Herbold is constantly looking for new employees and talents, whereby the embedding in a large, global group of companies facilitates the recruitment of specialists. Herbold can also score points with its favorable location in the attractive Rhine-Neckar region, flat hierarchies and a continuing familiar atmosphere among its 250 colleagues. And with the fact that a meaningful activity is carried out with head and hand.