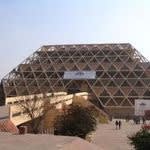
“The technologies we’re showcasing at Plastindia and the investments we’re making in our new Chennai facility demonstrate our commitment to our customers in India and throughout the SAARC countries,” said John Galt, Husky’s President and CEO. “With the most extensive service and support network in the industry, our new facility in Chennai will allow us to provide faster time to market and even better support to customers in this rapidly growing region.”
Plastindia marks the public debut of Husky’s H-PET AE (all-electric) preform manufacturing solution to the Indian market. Running at Husky’s booth (Booth M26, Hall 18) is a 32-cavity H-PET AE 180 workcell producing a 19 gram EcoBase™ preform for a 1 litre still water bottle application. Husky’s H-PET AE system is an efficient, affordable solution for the lower volume preform market that offers customers exceptional value and the high level of quality the market expects from Husky. H-PET AE is energy efficient, flexible, easy-to-use and has low maintenance requirements.
As a complete solution, H-PET AE includes a fully integrated resin dryer, mold dehumidifier and complete workcell infrastructure package consisting of both water and electrical distribution as well as a mezzanine. Its tight process controls and accurate mold tolerances, together with Husky’s EcoBase preform design, result in preforms that are up to 2.5% lighter than other lightweight preforms allowing molders to benefit from additional resin savings.
Also being shown for the first time in India will be Husky’s Ultra SideGate™ and UltraSync™ hot runners. Ultra SideGate offers molders the opportunity to horizontally direct gate parts that cannot be effectively gated with a regular nozzle. Husky’s UltraSync technology offers shot-to-shot and part-to-part consistency through precise stem closing. Husky’s Altanium® Neo2™ temperature controller, which comes equipped with an intuitive touch-screen interface and provides two to 48 zones of control, will also be on display.
The primary focus of the company’s new 5700 square meter Chennai facility is mold conversion as well as mold and hot runner refurbishment for local preform manufacturers. The Chennai site also includes a Technical Center, which provides a venue for Husky to work with customers to demonstrate and configure solutions to meet their requirements. With the opening of this facility, Husky has also expanded its engineering capacity for hot runners and preforms in order to handle increased demand from customers in the SAARC countries. This means reduced lead times and faster time to market which is a significant competitive advantage for these customers.
Finally, as part of its ongoing commitment to providing the most responsive service and support in the industry, the new Chennai facility features a local supply of spare parts to offer Indian customers rapid service and minimize downtime.