Another topic was common ground in many of the presentations: the excellent recyclability of thermoplastics compared to the more limited recyclability of thermoset fibre composite materials. Georg Käsmeier, Managing Partner with Forward Engineering, pointed out that the EU is looking to make the circular economy the norm as part of the Green Deal. "Now is the right time to shift from linear to circular thinking in your product development and to consider the recycling process as early as in the product design stage," he urged conference participants. As part of a study, his company compared the CO2 footprint in the production of a brake pedal based on primary thermoplastics, bio-based materials and recycled thermoplastics. The CO2 savings potential of using thermoplastics with recycled content was found to be significant. "We believe that thermoplastic materials have great potential in terms of sustainability. To leverage this, recycling processes now need to be established on an industrial scale. But we do see that this challenge is being addressed by industry," said Käsmeier.
Thermoplastic lightweight parts in one go
Due to the increasing importance of thermoplastics in lightweight, Engel has invested heavily in technologies and systems for processing thermoplastic composites in recent years. "We are the first company in the world to be able to offer a fully integrated process that starts with a UD-tape laying cell and finishes with a fully consolidated, overmoulded thermoplastic lightweight component," said Paul Zwicklhuber, development engineer Composite Processing at Engel, in his presentation. The tape laying cell relies on the pick-and-place principle. This means that tapes can be deposited and spot-welded together at three- to four-second intervals. Since the quality of the stack depends largely on the accuracy of the tape positioning, Engel has equipped the laying cell with a measuring system with high-resolution camera technology. Downstream of this there is a consolidation unit which consolidates the thermoplastic tape fabrics in the injection moulding cycle. Consolidation can be seamlessly integrated into the overall process, which significantly increases efficiency in the production of tailor-made tape solutions.
Engel organomelt is the core of the integrated process. Thermoplastic fibre composite prepregs such as UD-tapes and organic sheets are formed and functionalised here. Functional elements, such as reinforcing ribs or assembly elements can be over-moulded immediately after thermoforming using a thermoplastic from the matrix material group. This enables a highly integrated and fully automated production process, while at the same time the process simplifies recycling of the parts at the end of their useful life. The organomelt process is also used in Brose's door module production.
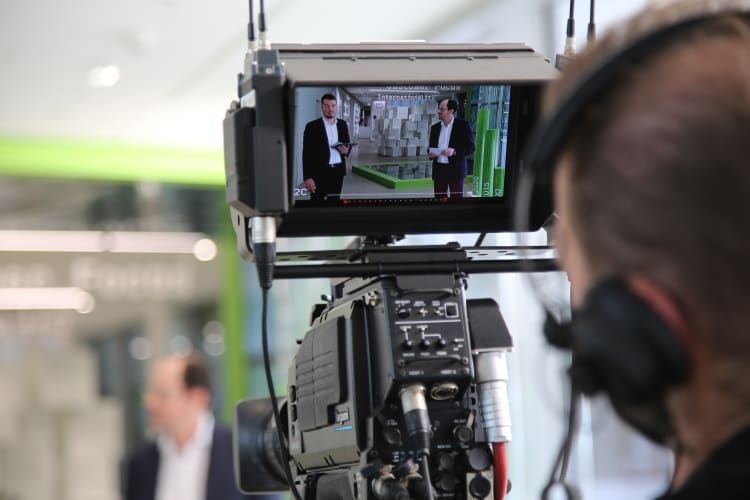
The Lightweight Future Day 2021 was held as a virtual event. For the coming year, the organiser, ENGEL, is again looking forward to welcoming participants on site. In 2022, the event is expected to take place as a hybrid solution that enables both on-site and virtual participation.
The use case of Swiss-based Svismold showed that lightweight materials can also still benefit advantages even if weight is not an issue. The company was able to convince a manufacturer of surfboards to replace the previous thermoset fins with a fin made of thermoplastic fibre composites based on UD-tapes. It turned out that the new fin offered unparalleled steering precision characteristics. One reason for this is the precisely calculated force flows in the part, which can be reproduced exactly in the part as the use of UD-tape ensures the fibre alignment, while at the same time reducing production costs. The surfboard with the new fin received an enthusiastic welcome from the surfing community.
An exchange is important – personally and across industries
The exchange of experience and knowledge between machine manufacturers and system suppliers, material suppliers, mould makers, researchers and developers is what makes the Engel Lightweight Future Day so valuable for the participants. On top of this, there is an exchange between industries which are otherwise totally different but are looking for solutions to similar challenges.
"Even though the virtual platform has achieved a particularly high level of coverage this year, personal contacts are still important for us," says Christian Wolfsberger. "We look forward to offering the Lightweight Future Day again next year as a face-to-face or hybrid event, and to welcoming as many participants as possible to our location in Schwertberg."