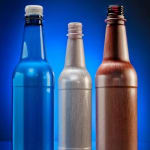
Plastic Technologies, Inc. (PTI) is now making its innovative oPTI lightweight foamed polyethylene terephthalate (PET) container blow molding process available for beer applications.
The process can be used to produce bottles in a variety of structural configurations depending on the brewer's shelf-life and marketing objectives. These include a monolayer PET version and two over-molded options (an oPTI inner layer and an overmolded traditional PET outer layer or a traditional PET inner layer with oPTI technology used to produce the external layer).
"Brewers continue to look for single-serve alternatives that provide product differentiation for on-premise, venue consumption. It's about finding a container that can deliver a strong brand message, while still achieving performance, cost and environmental objectives," explained Frank Semersky, vice president, chief innovation officer, PTI.
The overmolded options have been developed to deliver point-of-sale differentiation coupled with performance attributes at a cost significantly lower than single-use aluminum beer bottles. The dual layer structures also enable a customization of barrier attributes. For example, oxygen barrier can be added to the inner layer, while the outer is made with carbon dioxide barrier.
Further, the oPTI process pushes the door wide-open to developing visual aesthetics and tactile feel that have not previously been experienced in the beer category. You can use colorants in conjunction with either layer in the overmolded structure to achieve spectacular visual impact. Additionally, brand support via high embossing capability is possible when using the oPTI technology on the outer layer.
oPTI technology can produce bottles with improved light barrier when compared to traditional PET containers. Additionally, the foam process enables lightweighting of up to 5 percent without significant loss of performance.
Launched in 2009, the technology represents a departure from traditional PET processing approaches. The oPTI process is based on preforms made from MuCell microcellular foam injection technology licensed from Trexel, Inc. The bottles can then be blow molded on conventional, unmodified blow molding equipment using four basic steps:
- Nitrogen is injected into the melt through the barrel on a modified preform molding machine to form a single-phase solution of polymer and gas.
- Foam is produced as cavity-fill pressure is dropped below nucleation pressure during the injection cycle.
- Foam cells expand as gas diffuses into the bubbles. Processing conditions are used to control cell growth in the finished perform.
- Bottles are then blow molded.
In addition to PET, the foam bottle technology is applicable to other resins such as polylactic acid (PLA) and polyethylene naphthalate (PEN). Potential applications include a wide range of bottles and jars in food, beverage, personal care, household chemical, etc. markets.