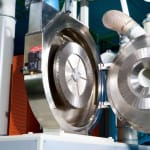
These are the features that mills made by the Pallmann Group offer in response to demands of masterbatch producers and compounders.
Polycarbonate, ABS, polyamide, polyimide, EVA - milling these materials into top quality powders for masterbatches and the like, without special cooling, is possible. Energy saving does not begin with fiddling with design details, but rather by asking basic process questions: processor who want to eliminate expensive cooling of materials with liquid nitrogen or other media prior to grinding, who can carry out quicker and deeper cleaning, who can put more materials through a mill in quick succession, and who can accurately target important parameters of the final product, will come out on top with considerable energy, cost and quality advantages.
Cost and quality are the focal points of masterbatch production. Special design features developed for Pallmann’s PolyGrinder mills target these aspects.
The state of the art in virtually every other mill on the market allows only Hart PVC and polyethylene to be ground at room temperature. Because the material heats up during grinding, air cooling alone is insuffi-cient with other materials. In most cases, liquid nitrogen is used instead. Costly to generate, store and supply, liquid nitrogen adds around 5 to 10 cents per kilo to the cost of the product.
It doesn’t have to be that way. Pallmann’s patented mill design can process "difficult" materials such as Ethylene vinyl acetate (EVA) with a VA content of up to 20 percent into high quality particles, without any extra cooling. And depending on the composition, the PolyGrinder has no problem with a polypropylene copolymer that no other mill on the market can handle. Processing costs benefit from the lower complexity of the system as well as the elimination of costly nitrogen.
The milling of a very wide range of plastics without additional cooling and with a defined particle shape is possible thanks to the use of some very special grinding wheels: instead of being made in a single piece, the profiled areas are in segments, which are better able to give an even scissor-like cut over the entire grinding area, creating a lower energy input - and thus reduced warming. The special cutting shape achieved with this construction not only protects the processed material, but also the mill: the reduced wear considerably extends the lifetime of the segments. In addition, the segmentation provides for lower cost of resharpening and increased safety. Ring-shaped components common in other constructions tend to warp during annealing, causing assembly problems.
Engineers prefer symmetry – and that makes sense in most plant and equipment. In this case, however, the patented, special arrangement of the fixed and moving grinding wheels works in a simple way to yield an important effect: the automatic air flow that results in the grinding chamber ensures an even and optimal transport of the material. Despite the compact design, a so-called large-chamber effect is achieved.