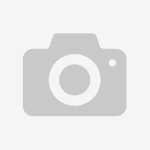
After successfully completing a restructuring process, a new and highly-flexible approach to injection moulding production, which was designed and implemented in cooperation with Engel, ensures improved competitiveness. The central aspect of the production design is that of restricting machine deployment to just two sizes, global use high speed mounting systems and standardization of machine/mould interfaces. Electrical connectors are very common standard parts! If this is your opinion before you visit one of the manufacturers of these industrial products, reality will soon teach you a different lesson. The real situation is completely different, as there is no such thing as a universally valid standard. This is caused by the need to observe national legislation and situations on the one hand, and the requirements of specific applications on the other. The consequence is a huge number of configurations and just as many connector types. No matter whether you need a connector for use in a dusty environment, in case of strong vibrations, in a moist environment, or in contact with chemicals – special configurations are needed for every single application.
- We manufacture up to 3000 connector variants, from simple 16 A wall sockets and matching plugs, through to heavy-duty 125 A connectors. Our range covers everything from industrial configurations to military specifications. Our mission, of serving the market as a full-range manufacturer, demands this kind of product diversity - says Dr. Gerald Sondermann, Director of Production, describing the situation, and adding the following while walking through the injection moulding production department: - As more or less 100 percent of our connectors and sockets are made of plastic, we have 500 ‘active’ injection moulds, and we manufacture 5 to 10 different plastic components with each one.
But this does not do justice to the company's product diversity. On top of different configurations, colour variants are required for standards compliance. In our assembly shop, we combine them with contact inserts and add-ons – which depend on the country and customers specifications – to finish the final connector variant.
In this environment, flexibility is the key to success – flexibility in both production and logistics. Optimisation, that is minimisation of the quantities of semifinished products kept in stock – is a major success factor. The consequence for parts production is a plant concept that guarantees a minimal response time to a product order. The search for this optimum concept was part of a major
restructuring process. Head of production, Sondermann: - We discussed the task with several injection moulding machine manufacturers, however, Engel gave us the most convincing answers, not least because they went far beyond the norm and showed us a fundamental change in our approach to production.