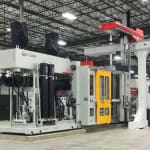
Ernsberger added, "Milacron worked closely with our entire team at 20/20 to identify the upgrades to the existing machines to be rebuilt that will put these machines above today's current machine specifications and give us the widest capabilities for these size machines in the industry." Ernsberger continued, "We also had Milacron integrate some proprietary technologies into their machines that allow us to have the most versatile LPIM Structural Foam machine fleet in the custom molding market. It's a great partnership between the companies, as all equipment at 20/20 CMP is 100% Milacron."
Milacron CEO Tom Goeke stated, "Stories like 20/20's machine retrofits reinforce the fact that Milacron has an unrivaled aftermarket offering. Our aftermarket offerings aren't only spare parts, we can literally take an older machine and transform it to like new condition. Milacron has set the standards, driven innovation and led the industry in Multi-Nozzle Low-Pressure Injection Molding Technologies for more than four decades. These machines can be used for Structural Foam, Structural Web, Gas Assist, Solid Molding, or combinations of these technologies depending on the application." Goeke added, "The LPIM market is strong for our customers that require either new or rebuilt machines in both North America and Europe, and we have a number of solid inquiries both domestically and internationally including many from Latin America and India."
Ideal for injection molding large, lightweight, durable structural plastic parts, the Milacron LPIM Structural Foam Technology creates a cellular foamed core surrounded by integral skins, forming a total integral and rigid structure. In this process, a foaming agent N2 is mixed with the polymer melt and short-shot through a modular multiple nozzle system into a mold (or multiple molds) in a volume less than is required to fill a solid part. The injection pressure and expanding gas/polymer cellular mixture act to fill the mold. The mold cavity pressures are 10 - 20 times lower than conventional injection molding which permits the use of lower cost aluminum molds with no hot runner since the hot runner manifold and nozzle system is integral to the machine. Many molds and large parts of different sizes can be molded at the same time. The multi-nozzle machine design allows for multiple molds to be run simultaneously allowing for higher productivity.