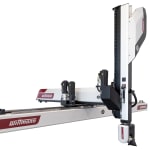
Available from June 2021: the upgraded WX153 robot from Wittmann - the ideal automation solution for injection molding applications on machines with clamping forces from 500 to 1,300 tons.
The new automation solution for injection molding applications in the medium and higher clamping force range is based on the newly upgraded WX153 robot from Wittmann. The system consists of a cartesian axial structure with a mobile X-axis serving as demolding axis.
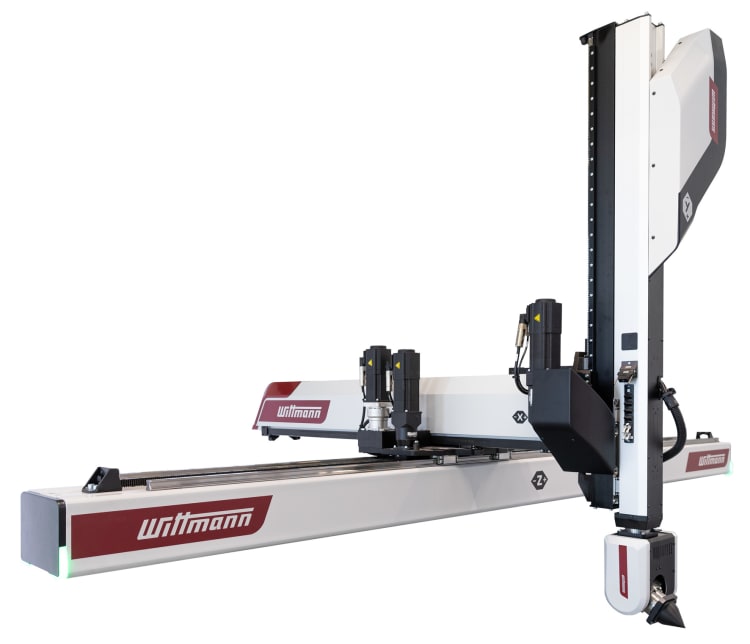
WX153 robot with servo rotation axis mounted on the vertical axis.
A horizontal stroke of up to 18 m and a vertical stroke of up to 2,600 mm are possible. An X-stroke of up to 1,400 mm is available for parts removal. This 1,400 mm demolding stroke provides a maximum reach of about 1,790 mm. In this context, the term “reach” designates the maximum distance between the horizontal axis and the mounting plate of the swivel axis at the lower end of the vertical axis. The reach is an essential parameter for the layout of robot systems.
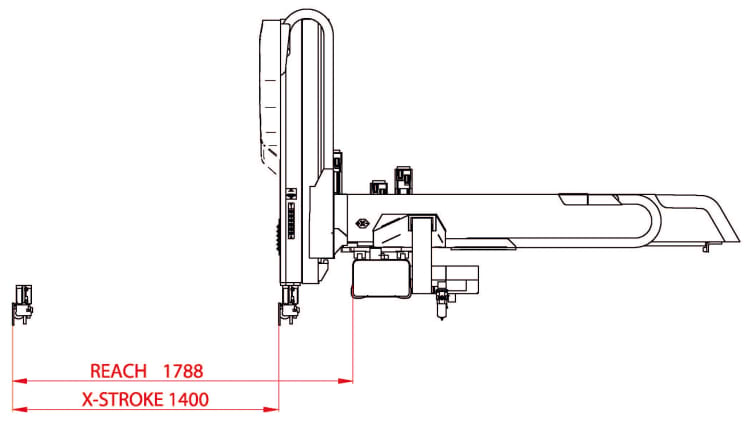
This diagram very clearly illustrates the difference between the reach and the X-stroke.
Internal tubing and/or wiring in the vertical Y-tube, easily accessible lubrication points and the integrated control cabinet at the rear of the horizontal carrier are part of the WX153 robot’s standard equipment. The control cabinet has invariably its original dimensions regardless of the number of additional axes attached.
Three additional axes can be mounted to each robot at the end of its vertical axis to drive the removal gripper. Moreover, Wittmann is able to build tandem robot solutions as well, that is, two traversing units acting together on the main carrier. Even in such cases, an add-on control cabinet can be dispensed with; so the space provided for it beside the injection molding machine can be used for any necessary auxiliaries other than automation equipment.
The WX153 robot to be shown by Wittmann in the first presentation by Wittmann Interactive in Viennan on 19 May is equipped with three additional servo rotation axes (A-, B- and C-Servo). In this way, synchronized 6-axis movements or less axis movements can be programmed, with the R9 robot control system from Wittmann coordinating automatically the speeds of the individual axes that have to be synchronized, so that all rotatory and translational motions are completed simultaneously.

Schematic diagram of additional servo rotation axes.
Various optimizations still enable the WX153 to operate with a gripper weighing more than 20 kg even when using three (!) additional axes. Compared to the previous device concept, this equals a possible increase in weight by more than 30 %.
The sales launch of this appliance with all of its options – including the new 3-servo-axes combination – is scheduled for June 2021.