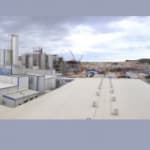
The US $200M expansion, comprising of two production lines with a capacity of 750 metric tons per day, employs the latest cutting-edge sustainable PET technology. Through the application of pioneering technologies the plant has been designed to yield the lowest available carbon footprint PET products.
OCTAL has already set new global benchmarks for both product and environmental excellence and currently uses 67% less electricity to manufacture DPET sheet and 38% less energy for PET resin. In addition, 80% of water used in the purpose-designed production facility is reused and all of OCTAL’s energy needs are derived from clean burning natural gas with its on-site high efficiency burners consuming up to 20% less gas than traditional PET plants. The integrated facility also has the ability to recycle trim waste during the manufacturing process and offers customers various recycling options.
States OCTAL’s COO William J. Barenberg: “This total integration of sustainability into our plant design gives us the ability to provide the global packaging industry with 927,000 tons per year of PET resin with a lower carbon foot print. We believe this will help encourage markets to migrate from less efficient materials to PET as the preferred clear rigid polymer.”