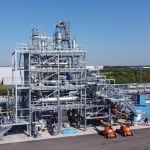
Non-recyclable plastic is one of the problems of the present. Various technologies ensure the re-use of plastic products and their separation in waste processing. But the loss rate incurred in this area is still high. In the first place, plastics cannot be recycled and re-used indefinitely. Secondly, separation of pure homogeneous materials often presents a problem which leads to large quantities of non-reusable mixed fractions. These are normally burnt or disposed of on landfill sites.
However, latest research findings have opened up a possibility to extract oils and fuels from this no longer usable plastic once more. In this way, the material cycle can be closed again by returning the oils gained by this method to the chemical and petrochemical industries.
The Dutch company Petrogas – Blue Alp, domiciled in Eindhoven, has developed a production plant for this process over several years and commissioned it for Renasci, located in Oostende, Belgium.
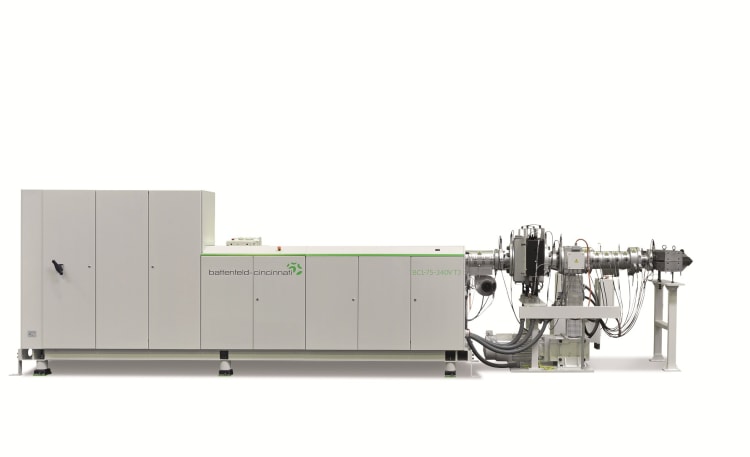
In this process, the starting material (used plastic) is first collected and shredded, then its ingredients are analyzed. Next, undesirable foreign substances are filtered out, and the material is dried. By renewed agglomeration, a starting material is created in the form of a granulate.
This granulate is melted by battenfeld-cincinnati high-speed extruders and degassed via vacuum zones. In this way, volatile foreign substances are extracted and pumped off separately. The high-speed extruder is particularly well suited for this purpose, since its compact design in combination with a powerful transmission drive ensures a high output. These two advantages were decisive factors in the design of the entire system. An additional benefit is this extruder model’s user and maintenance friendliness. battenfeld-cincinnati specially developed a new processing unit and screw geometry for this application.
Downstream reactor units then split up the melt delivered by the extruder into its individual components.
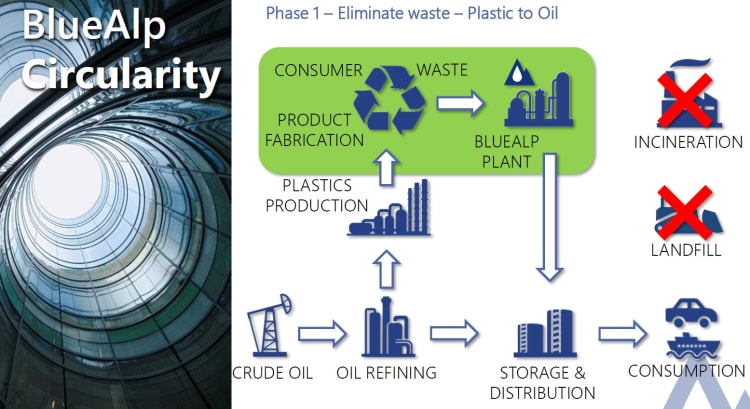