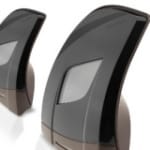
Dr. Bourdon, there is much talk of functional integration in injection moulding technology these days. But it is nothing new, is it?
Dr. Karlheinz Bourdon: People have been aware of the functional integration process for a very long time. That is precisely what multi-component technology is, and it is a long-established feature of injection moulding. I am convinced that new materials and new processes will now enable us to make major advances in functional integration too. We can combine other materials with the most varied manufacturing processes. That is what is genuinely new, what did not exist in this form before.
What are the limits to functional integration?
Dr. Bourdon: I don’t see any limits from a technical point of view. The question is always whether it makes economic sense. In the end, we are talking about the cost of making parts. If costs can be reduced by using functionally integrated parts or processes, they will be used, but not otherwise. In the foreseeable future we will be able to combine more materials, and that will open up completely new applications.
What does KraussMaffei offer that is new in this field?
Dr. Bourdon: Our focus recently has been on what we call the ColorForm process. This allows very high-quality surfaces with very different structures to be produced directly inside the mould. First, the thermoplastic substrate is injection moulded. Then a coating system is applied consisting of a polyurea or polyurethane PUR and the desired surface structure produced on the injection-moulded part. This is a multi-component injection moulding process where one of the injection moulded components is none of the usual thermoplastics but a PUR coating system. This is virtually a twofold functional integration. On the one hand we apply a high-grade coating to a component, while on the other we also combine two different technologies, the reaction process and the injection moulding process, in one machine.
The IMKS process (integrated metal/plastic injection moulding) is another excellent example of functional integration. At Fakuma, KraussMaffei will be using a CX 80 Hybrid to demonstrate how strip conductors with press and hold functions can be directly integrated into a thermoplastic component. We are not only combining two different materials but at the same time integrating their functions efficiently.
How many applications are you already using the ColorForm process for?
Dr. Bourdon: We are only just beginning to introduce this technology on to the market. But the motor industry is showing a great deal of interest in this process for both outside and interior applications. The next two to three years will show how many production-line applications there are. I am very confident that the ColorForm process will take hold quite quickly. But the applications are not limited to the motor industry.