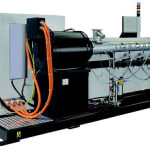
In pipe, profile, sheet and film extrusion, the energy costs constitute 3 to 5 per cent of the total costs, and consequently they are often the decisive factor in the cost-efficiency of the process. The extruder itself is considered the largest energy user in every extrusion line.
This is why battenfeld-cincinnati has already equipped all of its extruders with maintenance-free, energy-efficient AC motors as standard for several years. Tests have shown that torque motors offer a further increase in efficiency thanks to their high performance coefficient. This concept is already being applied in modern high-speed extruders. It should be remembered though that the operating range is a decisive factor for both motor types.
The nominal operating point where the drive yields its maximum efficiency should always be targeted. Optimized screw geometries for every application also contribute to saving energy on the extruder, as does tempering of the processing unit. Here, the machine manufacturer relies on concepts that are highly flexible, provide excellent contact with the barrel and offer a large surface for optimized heat dissipation. Therefore battenfeld-cincinnati takes great pains to advise its customers on their choice of the right extruder, and its comprehensive product portfolio includes the ideal equipment for every processing task.
However, optimizing only the extruder is not sufficient for sustainable energy consumption cuts on the entire extrusion line. So battenfeld-cincinnati offers an energy monitoring system to ascertain exactly how much energy each component of a complete line consumes. The system measures all energy flows in the line and compiles an energy distribution chart. Thus processors get an accurate overview of how much energy is being consumed at each point. This enables reliable comparisons on the basis of which practicable energy saving measures can be devised so that the production process becomes more efficient.
battenfeld-cincinnati has also focused on the energetic optimization of the downstream components for some time. Cooling and haul-off equipment and cutting devices have been continuously improved to achieve more efficiency.
One of the latest innovative developments is the Green Pipe downstream concept, which has significantly improved the energy efficiency in cooling pipes. Instead of conventional cooling baths, where every spray tank operates with a separate water circuit, the Green Pipe system has all spray tanks connected to each other, so that the water is pumped through all tanks from the last back to the first according to the countercurrent principle.
This raises the return temperature to the cooler significantly, which increases the scope for making use of free cooling. This in turn reduces the load on the compressor and consequently the delivery rate of the pump. The temperature level of the waste heat is also raised sufficiently to permit exploitation of the waste heat for energy reclaim.
This shows that battenfeld-cincinnati offers not only efficient extruders but also a holistic concept to save energy and thus a sustainable cost cutting solution in the extrusion process.