
Sumitomo (SHI) Demag Plastics Machinery GmbH will unveil its fastest, most energy efficient, sustainable, data driven integrated machine line-up at K-2019. Presenting five machines, the company is continuing its staunch focus on delivering “Precision. Power. Productivity.” to plastic moulders globally.
Having reported another double-digit (13%) turnover increase after modernising its production and sales approach last year, Sumitomo (SHI) Demag will unveil five energy efficient machines. In addition, the company will launch a new eMultiPlug innovation, showcase its technical prowess in Liquid Silicone Rubber (LSR) moulding, plus provide an interactive area where customers can test out the latest smart diagnostic and support services using myConnect. With all this on display, K 2019 promises to be the unmissable plastics exhibition to round off the decade.
CEO Gerd Liebig comments: “Sustainability, productivity, energy resources, plastic waste, Industry 4.0, big data, automation -these have all been headline topics over the past ten years. As we race towards the end of the decade, Sumitomo (SHI) Demag is celebrating some significant milestones and showcasing how we are assisting moulders to tackle these topical circular economy and efficiency challenges.”
For Gerd, K-2019 marks the start a new era for plastic manufacturers. As well as new medical device and packaging legislation to comply with, European moulders have been contending with the plastic backlash, while attempting to navigate the circular economy, maintain business productivity, support the switch to eco-cars, plus factor-in labour skills shortages.
Despite the challenges, Sumitomo (SHI) Demag has continued to invest resources and R&D developing the most dynamic, high speed, sustainable and precise moulding machine line up to-date. All will be unveiled in Hall 15, Booth D22. Here’s what’s coming:
Smarter customer support services
Industry 4.0 provides an opportunity for plastic manufacturers to obtain and act upon detailed insight gathered frommachinery data. Through the use of connected devices, production managers can better manage inefficiencies, reduce costs, improve Total Cost of Ownership and minimise machine downtime.
At K 2019, Sumitomo (SHI) Demag will unleash the future of smart services, presenting a connected cell featuring the latest remote disgnostics, online support, document tracking and spare part ordering. Visitors to K 2019 will be able to use connected terminals to see how myConnect software will enhance customer service and be a launchpad for future data-driven efficiency improvements.
Andreas Holzer, Director Customer Service at Sumitomo (SHI) Demag comments: “Not only have our moulding technologies advanced to a level that delivers fast cycle times, unparalleled process stability and market-leading energy efficiency, now we can offer customers end-to-end processing traceability and the ability to monitor and reconcile data from numerous machine sources. Machine uptime, productivity, traceability and decision making can all be enhanced by deploying real time visibility. In addition to enhancing customer service response times, this seamless connectivity will be integral to future productivity in moulding facilities worldwide.”
Two energy-enhanced El-Exis SP addressthe packaging agenda
Consuming up to 20% less energy than its predecessors, Sumitomo (SHI) Demag is bringing two energy-enhanced El-Exis SP machines to K-2019 -a large and a smaller version. Catering specifically to the packaging moulding markets, the ultra-high speed range ensures manufacturers never need to compromise on quality, production efficiency or sustainability.
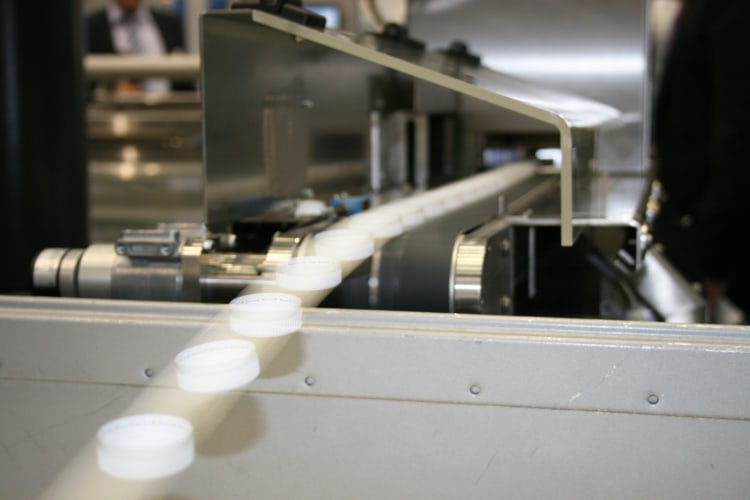
In a live demonstration at K-2019, Sumitomo (SHI) Demag will produce the equivalent of 130,000 water bottle caps an hour on a 72-cavity mould on an El-Exis SP
“Capable of delivering the lowest dry cycle times, the machines in the latest series have high process consistency and high energy efficiency,”explains Arnaud Nomblot, Director Business Development Packaging at Sumitomo (SHI) Demag.
Central to the machine's fast cycle time is the hydraulic accumulator, which achieves injection speeds of up to 1000 mm/s. This enables moulders to produce even thinner packaging items. The range is also one of the fastest machines in the market for injection dynamic. “The combination of speed with high quality moulding repeatability helps to minimise packaging production waste,”adds Nomblot.
High-tech touchfoil automotive consoles produced on new IntElect 500
To make driving more comfortable for motorists, at K-2019, Sumitomo (SHI) Demag will demonstrate a trailblazing, as-yet unseen, touchfoil interactive decoration for a vehicle console on a brand newIntElect 500 being unveiled at the show.
Ranging now up to 500 tonnes, the new IntElect series combines precision, energy efficiency and much larger mould space. As a result of the big tie bar spacing, increase in mould height and opening stroke, the new IntElect models accommodates larger moulds, providing a less energy intensive machine for automotive applications that would previously have required a larger tonnage.
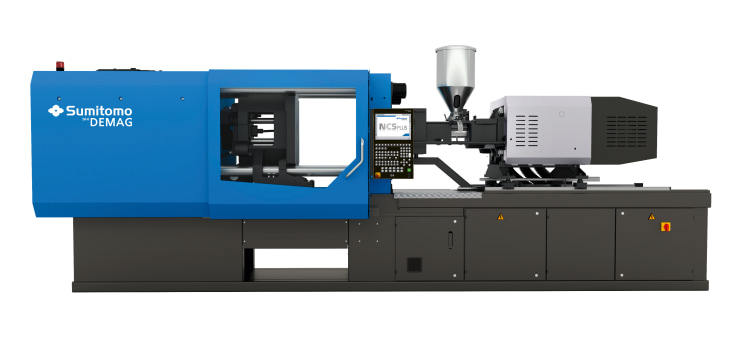
The new IntElect 500 can accommodate larger moulds, providing an alternative, energy efficient option for automotive applications that would previously have required a larger tonnage
“All of the technological enhancements in the IntElect 500 are designed to give moulders the tools, machine synchronisation, mould safety and real-time production monitoring required for tomorrow’s automotive smart factories,”emphasises Henrik Langwald, Business Development Director Automotive at Sumitomo (SHI) Demag.