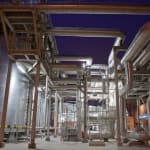
Among many imperatives we established for ourselves was a commitment to supporting our customers meet the increasing demand for verifiably sustainable products and to thereby reduce their own environmental impact. We achieved this by producing a high performance packaging material with the lowest available carbon footprint.
In doing so, Octal designed and currently operates a "unique-to-the-world" manufacturing facility. Our "Direct" PET sheet technology (DPET) has succeeded in consistently providing the industry with a material offering a lower carbon footprint compared to plastic alternatives.
Conventional PET manufacturing, which depends on as many as five reactors and requires separate processes for resin and sheet production, is energy intensive.
When building our process, Octal committed to reducing its overall energy use. We accomplished that by implementing the latest 2R reactor system to efficiently produce quality PET resin from only two reactors. In doing so Octal's resin-making and DPET manufacturing processes require substantially less energy in comparison to conventional processing. DPET's lower carbon footprint is a direct result of Octal's patented melt- to-sheet technology. Compared to traditional plants, Octal's DPET sheet uses 67% less grid electricity per kg of sheet.
Through proprietary software programs and process control technology, Octal maximizes roll-to-roll uniformity in every batch for DPET and achieves a caliper variation of 1%. This is a significant achievement given that industry standards vary around 5% (based on caliper control of 4-5%+ 8% flow of material). Customers can therefore reduce costs by ordering thinner gauge sheet while knowing exactly how much packaging they can manufacture from the material they buy.
DPET's unique process results in 3% to 8% more resin in deep corners and fine features, accomplished through its excellent flow characteristics in the mold. This allows designers the flexibility to achieve a better package designs that retain their shape in even the deepest and most intricate applications. More material in critical spots means one-for-one down gauging can be realized without blowouts or holes in the container walls.
Octal is positioned only a few hundred meters from the Port of Salalah, a world-class transshipment hub catering to the world's leading shipping lanes. Octal has set itself up to operate in such a way that it can service the supply needs of its global manufacturing customers with plants around the world from the highly efficient production location in Salalah. This is not only a competitive advantage with cost saving opportunities for customers - it is a streamlining of shipping requirements which contributes to a reduction of the carbon footprint via optimization of transportation.
In early 2011, Intertek Expert Services, an internationally-recognized, independent testing service, generated a carbon footprint of Octal DPET sheet and compared the results to other leading alternative plastics. The study considered all emissions related to the production of resin and DPET at the Octal Salalah facility in Oman, and established a carbon footprint characterizing the delivery of Octal resin and DPET sheet to the United States.
In its evaluations, Intertek employed as its standard the Greenhouse Gas Protocol (GHG): the most widely used international accounting tool for government and business leaders to understand, quantify, and manage greenhouse gas emissions.
The GHG protocol classifies according to direct and indirect emissions. The direct emissions are those, which are directly emitted by the organizations that are reporting under the GHG protocol. The indirect emissions are those emissions, which are emitted by organizations from which the reporting organization purchases goods, energy and services. Accordingly, all companies under analysis are categorized as to their ability to comply with three sets of criteria called "scopes."