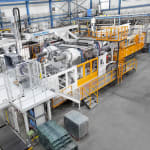
Containers for today's logistics have to be stackable, feature IML barcodes, integrated RFIDs and, of course, the logo of the company that owns them. Switzerland's Georg Utz AG has specialized in this application, and for this reason it has commissioned the country's largest injection molding machine, a KraussMaffei MX 4000-75000. At eight locations on three continents, Utz produces high-quality products for in-house and external logistics.
Big move: The heavyweight machinery traveled on a total of 22 trucks from Munich to Bremgarten (about 15 kilometers west of Zurich): one for the machine bed, each platen, one per two tiebars and one each for many other components. After 12 weeks of set-up, the MX 4000 went online on the requested target date and replaced an older machine with a clamping force of 27,000 kN that was energy-inefficient, offered limited technical options, had only a simple linear robot and had insufficient energy efficiency.

National record: with a clamping force of 40,000 kN, the KraussMaffei MX 4000-75000 is Switzerland's largest injection molding machine
Cycle time-optimized automation with large working radius
The new model features a sophisticated two-story automation system that implements the subsequent process steps such as the application of RFIDs, IML barcodes and logos plus post-processing and quality assurance within the cycle time. The two KraussMaffei LRX robots right at the machine have twelve-meter-long Z-axes and thus a particularly large working radius.Utz will take advantage of the ability provided by the MX 4000 to use stack and multi-cavity molds and thus increase production volume. The globally active family-owned company runs three shifts at its plant on the new MX 4000, producing approximately 20 different products with weights of up to 50 kilograms, including pallets, boxes and Paloxes. The material is usually a polyolefin such as PP or HDPE, but ABS or technical plastics are also sometimes used.
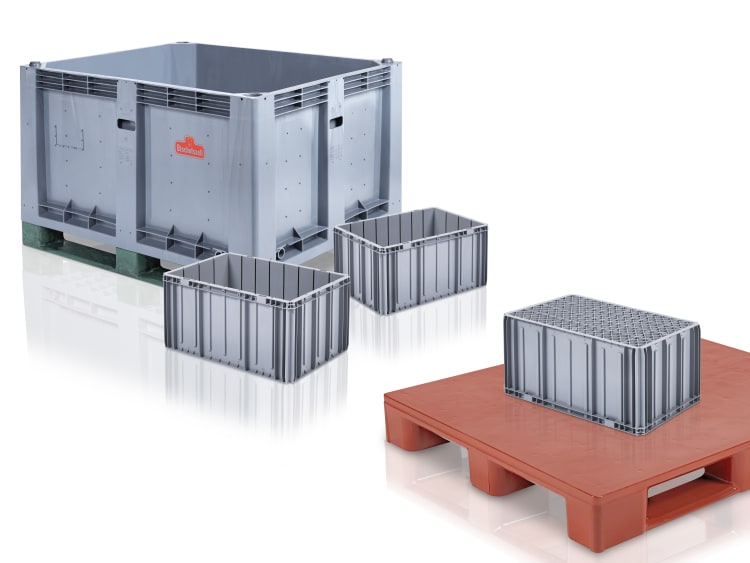
Loaded with extras: Today's pallets, boxes and PALOXEs manufactured on the MX 4000 have to do more than hold goods. They are moved by storage robots and feature IML barcodes, integrated RFIDs and, of course, the logo of the company that owns them
Increasing use of recycled material
The percentage of recycled material is currently 35 percent and Utz operates its own recycling sites for this purpose, for example a mill in Switzerland with a throughput of 1.2 tons per hour. Plans call for the percentage of recycled material to increase to 80 percent as part of the Utz Group's global climate strategy. This is where one function of KraussMaffei machines plays a special role: APCplus. Based on the melt viscosity, APCplus controls the changeover point and the holding pressure level and thus ensures parts with extremely consistent weight. This balances out batch fluctuations that result from different raw materials and percentages of recycled material.Andreas Schlegel (Head of Operations / Managing Director at Georg Utz AG) the important factor is that this opens up a wider gateway for material purchasing. In the case of regrind, for example, it is also possible to buy different quality grades or polyolefin blends that are more readily available. APCplus has been being used on the smaller machines for two years, and in this time, scrap has decreased significantly.
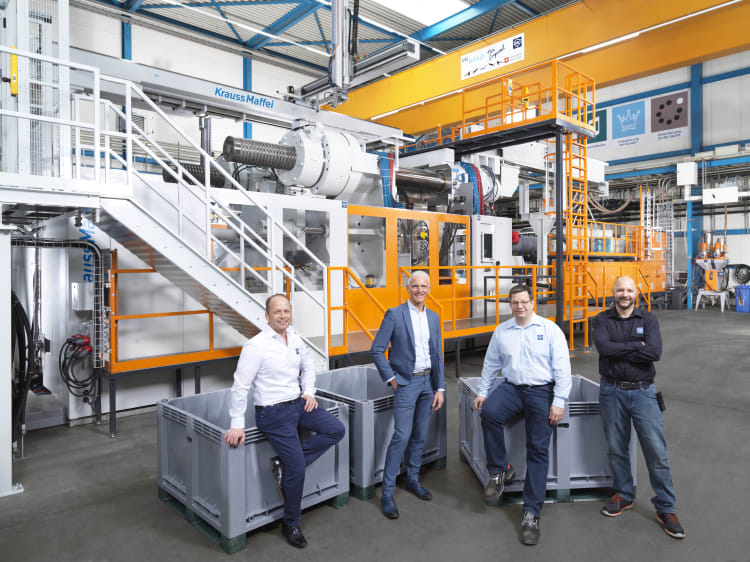
Holding mutual trust and collaboration in high esteem (from left to right): Andreas Schlegel (Head of Operations at Georg Utz AG, Member of the Management Board), Bruno Schleiß (Managing Director at Krauss-Maffei (Schweiz) AG), Marcel Meier (Head of Production Technology Georg Utz AG) and Markus Eggimann (Head of Production, Georg Utz AG)
Digital research project
Utz is currently using another of KraussMaffei's digital products to develop a predictive quality solution in collaboration with the Institute for Materials Technology and Plastics Processing (IWK) of the Eastern Switzerland University of Applied Sciences. The DataXplorer can save up to 500 signals per second from the machine and other sensors and display them as curves. The goal now is to determine how many of these are needed in order to predict good components reliably.
As a global player, Utz has over 1350 employees and state-of-the-art production locations in Germany, England, France, Poland, China, the USA and Mexico. The company is headquartered in Switzerland. The group operates a total of 50 injection molding machines from KraussMaffei, 22 of which are running in Switzerland at clamping forces starting at 800 kN. With an export share of around 40 percent, Utz Switzerland delivers its products primarily to Italy, Austria, Eastern Europe, the Scandinavian countries and Oceania.