The recycling practice available today is based on waste recovery, sorting, cleaning and mechanical recycling. The final result, the quality of the regranulate, depends on the quality, purity and homogeneity of the waste. The more homogeneous, the better selected and the cleaner the waste, the more likely it is that the final result will be a plastic regranulate that is easy to use and has a small variation in terms of physical parameters.
Based on the above, it is easy to come to the conclusion that a sufficiently sophisticated selective waste management system, appropriate logistics and adequate recycling capacities can theoretically serve the diverse needs of the plastics industry.
In theory, yes, but it must be taken into account that, for example, the weight of one roll of polypropylene film produced in the largest quantities can exceed 100 kg, while the collected candy or chocolate packaging material is only a few grams. This conclusion does not take into account the fact that the place of production and the place of use of the finished plastic product are different. A good example of this is BOPP, where barely 10% of Hungarian BOPP production is consumed domestically. Of course, anyone who has enough imagination and can imagine a waste collection, treatment and logistics system that manages these problems in a larger geographical region, for example in Europe, and optimizes and manages waste streams. However, neither imagination nor regulation can overcome the laws of MFR changes during recycling.
In the case of polypropylene and polyethylene, even in the case of the original, so-called virgin polyethylene processing, a significant degradation takes place in the polymer macromolecules, during recycling the polymer chains are further subjected to thermal shock and shear. The molecular weight decreases and the flow rate increases. Practically, this means that an originally split fiber of MFR[2]3-4.2 - typically the raw material of woven bags - mostly an injection grade with a flow rate of MFR 5-6-7-8 can be made. The flow rate and the processing procedure are also changed at the same time. With each recycling cycle, the flow rate continues to increase and the area of use narrows, until finally, after a few cycles, we get regranulate that can't be used for anything. Of course, it is possible to reduce the degree of molecular degradation and flow rate increase with additives and a gentle processing method, but one thing can be said for sure regarding the polyolefin plastics used in the largest quantities: mechanical recycling cannot produce regranulate suitable for the production of finished plastic products of the same quality as the original waste. It can be regranulate, for which you have to find the appropriate field of application. The problem is that in areas of application characterized by a lower MFR, the consumption of "virgin" garnulate is higher than in areas with a higher flow rate. In the case of polypropylene, we manufacture the majority of fibers and films under MFR 4, as well as pipes, which is almost half of domestic polypropylene consumption. These are typically continuous technologies, i.e. one or a small number of high-capacity machines continuously emit the product. Polypropylene grades with a higher flow rate are typically used in injection molding technologies, which are batch-technologies and produce plastic finished products that can be measured in pieces.
The essence of the problem is that we cannot provide regranulate for plastic products characterized by a low MFR. Until then, there will be a significant oversupply in areas with a high flow rate. In other words, there will be no regranulate for polypropylene films and raffia fibers, while there will be an oversupply in the field of injection molded products. The currently used mechanical recycling based on selective waste collection can only be a solution for 25-30% of polyolefin-based plastic grades. What next? Is 2025 very close?
One of the solutions is the production of virgin-recycling compounds, but this is also based on mechanical recycling, which requires high-quality waste. The addition of overcompensated virgining polymer can reduce or even compensate for the increase in MFR, but cannot compensate for the degradation of the polymer chains and molecules of the added regranulate. This means that by adding various additives, we can achieve that the physical parameters of the virgin-recycling compound are like "new", but this can only be achieved by using a significant amount of additives. Is that the goal? Using even more additives? Filling the so far "clean" polyethylene and polypropylene films without dissolution with even more compounds?
Chemical recycling will play an important role, which for now mostly means pyrolysis. However, the plants are still in the pilot phase. This means that a fraction of the required capacities, less than 1%, exist. The technology is not yet mature, and we only have guesses regarding the total carbon footprint. It will be available on an industrial scale only in the second half of the 2030s. Europe alone would need to build several million tons of capacity.
Between 2025 and 2030, it will be clear that our targets for mandatory recycling rates are illusory. The plastics industry will not be able to meet the 25% recycled content requirement by 2031.
[2] MFR - Melt Mass-Flow Rate (230°C, 2.16 kg)
Author: László Bűdy, Polimer Market Analyst - Central Europe
What next?
Let's live without plastic packaging - let's make a year-long plastic-free July? Many people would certainly be happy with this, for a week. But I draw the attention of everyone to the fact that there is a packaging machine at the end of every production line. If the packaging machine stops, production must also stop. Plastic is a feature of today's globalized world, without it the current industrial and agricultural structures would not function, and even the urban way of life would be impossible. We have to reckon with the tyranny of the melt flow rate, we have to live with it. It forces us to set achievable and sustainable goals. We must ensure that legislators do not want to override the laws of physics and chemistry.
We will discuss this question at the Central European Plastics Meeting (www.plasticsmeeting.com) September 19-20 2023, Budapest.
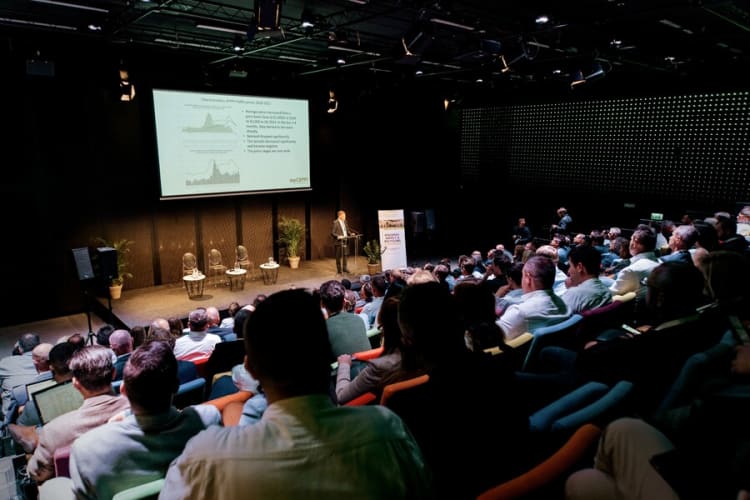