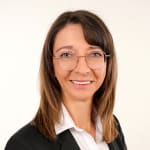
Europe wants to be climate-neutral by 2050 – and the circular economy for plastics will make a telling contribution. The core element of the EU Packaging and Packaging Waste Directive is the recycling rate. By 2025, member countries must recycle at least 65% of their packaging waste, which will increase to 70% by 2030.
The production of goods and commodities generates harmful emissions that increase the natural greenhouse effect. This inevitably leads to temperature changes with far-reaching consequences for the climate. Greenhouse gas emissions must therefore be reduced by at least 55% throughout Europe by 2030, and Europe intends to be climate-neutral by 2050. “The circular economy is one of the tools that can be used to achieve these goals,” says Martina Schmidt, who heads the Recycling and Waste division of Vecoplan AG. Vecoplan is one of the leading suppliers of machinery and equipment for processing primary and secondary raw materials for thermal and material recycling. “In the field of product design and packaging, using recycled plastics offers many possibilities for substitution,” says the Vecoplan expert. “According to the UMSICHT study by the Fraunhofer Institute, climate-damaging greenhouse gas emissions can be reduced by up to 50% if recyclate is used instead of new granulate from crude oil. We have to leverage this potential.”
However, recycling is not only crucial for climate neutrality, it also conserves valuable resources and the environment. A wide range of industries in the plastics industry are undergoing a transition. The aim is to increase the recycling rate and use the advantages of plastic in such a way that no damage is caused to the environment. The increasing demand in the various industries is leading to a tense supply situation and acting as a price driver. “We’re seeing a clear trend towards increased demand for high-quality plastic recyclates. Many manufacturers are closing their cycles because that enables them to influence this demand and deal with it,” explains Martina Schmidt.
Taking recycling into their own hands
Processors can quickly and cost-effectively satisfy the demand for high-quality recyclates by taking reprocessing into their own hands and following a holistic approach. “We work closely with our customers in developing our solutions,” says Schmidt. “In the past, processors always came to us with new challenges, which motivated us then - and still does today - to actively shape this change.”
The shredding of the materials is particularly challenging. For example, yarns, fibres and filaments are available in different thicknesses, in various and often extreme lengths and are made from various plastics. However, despite all their differences, they also share some unique mechanical properties - they are tough, wear- and tear-resistant and very elastic - which makes shredding all the more difficult. “A homogeneous output material is optimal for all downstream processes,” explains Schmidt. “That’s why excessive lengths and fine particles should also be avoided because they can cause disruptions or losses during the process.” In addition, to ensure effective downstream processing of the plastics, the characteristics of the input material must not be changed by the heat input that arises during shredding.
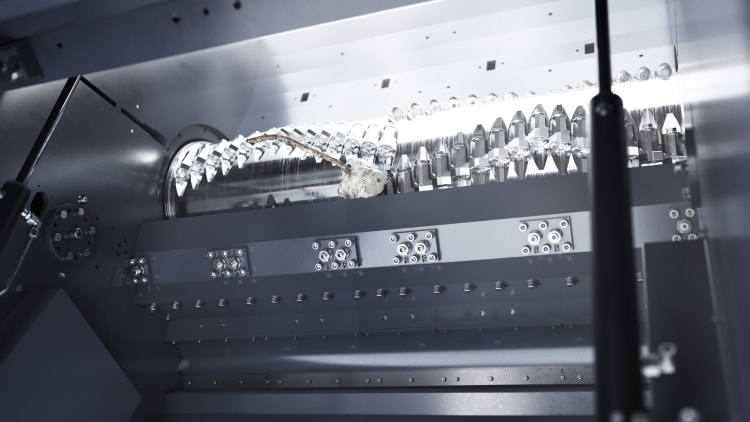