Focused on energy efficiency
Vecoplan relies on its exceptional HiTorc drive to achieve the best possible energy efficiency during shredding. Thanks to eliminating mechanical drive elements such as belt and gear drives, flywheels and clutches, the direct drive is 10-15% more efficient. The HiTorc is dynamic, has a strong start-up phase, is low-maintenance and is insensitive to extraneous materials. Even one unscheduled plant stoppage caused by a broken shaft, burnt overload clutch or defective gear is enough to justify using a HiTorc drive since it significantly reduces maintenance work and downtimes. “Our HiTorc is the Tesla among today’s drives,” says Martina Schmidt.Technology is key
Achieving the optimal coordination for the case at hand then continues with the selection of the ideal cutting unit, and here Vecoplan technicians work closely with their customers. “We develop shredders, which we individually coordinate through many tests in our technology centre. The test results are documented, made available to the customer and included in our database,” says Schmidt. The database now includes more than 3,000 tests. Output material temperature, noise emission, torques and cutting forces are monitored and recorded in real time. Vecoplan also has an in-house laboratory for measuring moisture, testing material and determining grain & density. “In recent years, we’ve developed an enormous level of theoretical and above all practical knowledge,” says Schmidt. Simple maintenance and the greatest possible ease of operation are essential aspects of all developments.En route to the perfect system
Is there a perfect machine? Martina Schmidt thinks about that for a moment. “To answer this question, we first have to define what we mean by a perfect machine.” Is it a shredder that’s correctly configured for the usage scenario? And can it handle a few measures such as adjustments to the cutting force, a changed cutting geometry or output ? “Our shredders offer a high degree of flexibility to meet these requirements,” she says.
Or should a perfect machine ensure stable processes and produce consistently high throughput and a homogeneous output material at all times? “Our customers also trust us to provide them with these machine features too,” says the Vecoplan expert.
“However, let’s not forget that sustainability is playing an increasingly important role. For example, how the possibilities of digitalisation can be exploited to add value for the customer, such as in the context of new business models. That’s what we’re working on.”
A powerful solution
To meet the high demands for the recycling of very different materials, Vecoplan revamped its proven, successful VAZ shredder series with the latest benchmarks in industrial design – and presented the series for the first time at IFAT in May. The modular design of this single-shaft shredder particularly convinces users. “It allows operators to use the series universally and get the right answer for a wide range of applications,” promises Schmidt. “We have many options for configuring and adapting the machine to the task at hand. These choices and the relevant combinations are critical to the performance and quality of the shredding process.”
The new shredder is also equipped with the Vecoplan Smart Center (VSC), Vecoplan’s powerful digitalisation concept for the maximum efficiency of shredders and systems. The integrated and intuitive VSC.control operating panel serves as a communication medium for the cutting-edge control of the machine and direct communication with Vecoplan. VSC.connect enables users to network their machines and access additional online services, such as remote service, key performance indicators and even a media database.
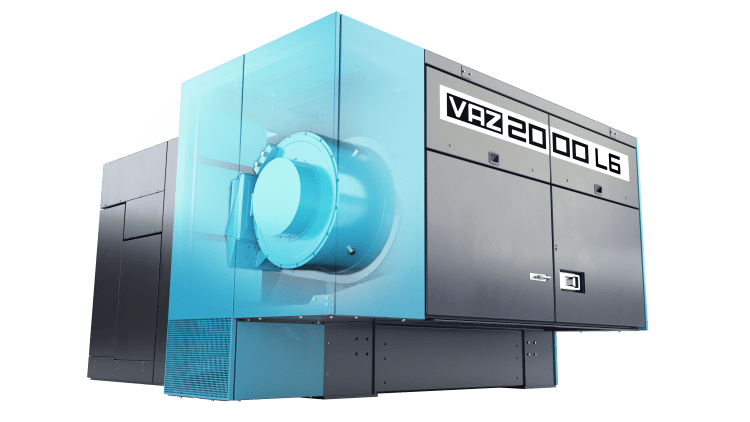