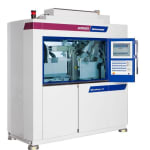
Medical technology competence
On a MicroPower 15/10, a machine which was specially designed for the production of small and micro parts, venous clamps made of POM with a part weight of no more than 0.003 g will be manufactured with a 4-cavity mold supplied by Microsystems UK within a cycle time of only 4 seconds. The parts are removed by a W8VS2 Wittmann robot and passed on to a camera integrated in the production cell and in the machine's control system for quality inspection. The parts are subsequently separated according to cavities and stacked in a stacking module. The parts are all injected, quality-inspected and deposited inside the clean room.Another application from the medical technology sector will be demonstrated on a machine from the servo-hydraulic SmartPower series. On a SmartPower 120/525, Wittmann Battenfeld will show the production of insulin pens from PP in a 48-cavity hot-runner mold supplied by Hasco, Austria.
Multi-component technology on an EcoPower with insider
The compact design of the EcoPower injection units favors the use of the all-electric machines from Wittmann Battenfeld for 2C injection molding. In combination with an insider automation system, a highly compact and user-friendly production cell is created. The robot installed on the machine can be pushed aside for mold change in just a few easy steps.On an EcoPower 180/350H/350V, a flange made of HDPE and PA will be produced using a 1+1-cavity mold supplied by Polar-Form Werkzeugbau GmbH, Germany. The insider cell incorporates a W821 robot from Wittmann for parts removal and depositing, as well as a Wittmann temperature control system and a conveyor belt.
Organic sheet application on a large machine from the MacroPower series
On a MacroPower 450/2250 an "organic sheet" component will be produced with a single-cavity mold from Georg Kaufmann, CH. This is a demonstrator part to illustrate the potential of this technology. The mold is equipped with a hot runner with needle shut-off, an edge folding slider for in-mold forming of the organic sheet and a punching die to punch out an aperture in it. The automation system developed by Wittmann Robot Systeme in Nuremberg is custom-made for this application and comes with a station to feed the organic sheets cut to size, a heating station to heat the organic sheets with heating elements supplied by Krelus, CH, a multi-functional gripper with a needle gripper to pick up the heated organic sheet, a suction unit for finished parts removal and a Wittmann robot W843 pro. The W843 pro positions the natural fibre mate in a heating station via the integrated B-C servo rotation axis. After the heating-up phase, the W843 pro removes the mate and puts it into the fixed part of the mold. Afterwards, it takes the finished part from the ejector side of the mold and places it on the conveyor.Extreme energy efficiency even in standard versions
The exhibition program will be rounded off by a SmartPower with 600 kN clamping force and an EcoPower with a clamping force of 3000 kN. On the SmartPower 60/210, a pump head will be manufactured from PP with an 8-cavity mold from Hasco, Austria.All machines will be loaded by a central conveying system from Wittmann.
Wittmann automation and peripheral equipment
In addition to the robots and peripheral equipment integrated in the injection molding machines, Wittmann Battenfeld is presenting a broad range of robots and peripheral equipment as stand-alone solutions.Exhibits from the automation sector will include robots from the new Wittmann Pro series, in particular the models W833 pro and W843 Pro. The Pro series models feature compactness, user-friendliness, a high degree of energy efficiency and conservation of resources, plus a low noise level. In addition to these models, a traditional W818 robot will be on show as well.
From the peripheral equipment sector, material dryers from the Drymax E and Drymax Aton series will be exhibited, as well as conveying equipment from the Feedmax series and Tempro temperature controllers, all from the Wittmann group. Among the dryers, the drying wheel dryer Drymax Aton should receive special attention. This dryer consists of numerous separate chambers loosely filled with desiccant balls. In conjunction with the innovative 3-save process, this not only ensures efficient use of energy, but also a continuous drying process with a constant dew point. Moreover, the use of conventional desiccants instead of honeycomb wheels permits low-cost exchange of the desiccant without having to replace an expensive, complete wheel.
On a separate display board, the Wittmann group’s solution for integrating robots and peripherals into the Unilog B6 machine control system will be demonstrated, which was introduced to the market under the name of Wittmann 4.0. Via the machine’s control system, several machines as well as robots and peripherals connected to them can be linked together and operated via the uniform Windows user interface, which enables interaction between the individual appliances. In this way, the entire manufacturing process, including material feeding and blending, temperature control, automation and injection molding can be optimally coordinated and tracked.
In Mexico, the Wittmann group is represented by its own sales and service subsidiary, Wittmann Battenfeld México S.A. de C.V. in el Marqués Querétero.