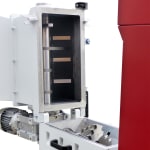
A Wittmann S-Max 3 screenless granulator with optionally available built-in feeding shaft offers many advantages. The feeding shaft helps to avoid bridging, especially in case of grinding long runners and flat parts.
Compared to conventional blade granulators, screenless granulators provide a number of benefits such as energy efficiency, less noise, clean and uniform regrind from hard, brittle plastics such as, ABS, PC, ABS+PC, PA, and reinforced plastics.
The granulator motors have a high tourque, the units run smoothly at a low speed (27 upm @ 50 Hz) without stalling, and they are suited for cutting thicker sprues and/or parts to a pellet size from 4 to 10 mm.
Advantages of feeding shafts
An additional feeding shaft – as offered as an option for the Wittmann S-Max 3 granulator – keeps large runners/parts in motion, and pre-breaks them, thus helping to avoid bridging or nesting of parts. The shaft also helps to avoid downtime eventually caused by material backing-up or material overflow, and keeps the production process running smoothly.
The optional Wittmann feeding shaft is independently driven and has elongated hooks to pre-cut the parts/runners and push them into the cutting chamber for a regular grinding, after the shaft has reduced the dimensions of the parts – and this may allow the use of an altogether smaller type of granulator, possibly saving capital expenditure.
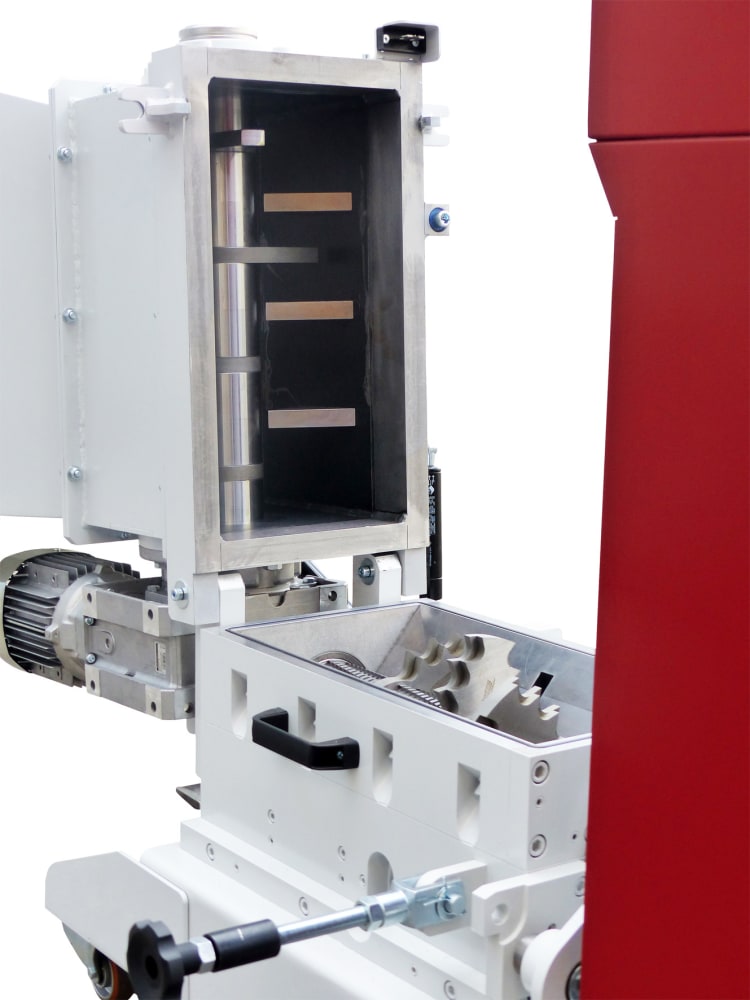
The opened material hopper of the S-Max 3 allows to take a look at the additional shaft from below.