Teile mit hohem Glasfasergehalt problemlos mahlen
Angüsse und Produktionsabfälle wie Anfahr- und Ausschussteile werden inzwi-schen an den Spritzgießmaschinen in Boxen gesammelt und von den Maschinen-bedienern zum neuen Recyclingcenter gebracht. Dieses befindet sich im Zentrum der Spritzgießhalle und besteht aus vier neuen S Max 2 Mühlen von Wittmann. Für die Hauptmaterialien und Farben gibt es vor den Mühlen jeweils eine eigene Gitterbox. Die strikt sortenreine Sammlung der aufzuarbeitenden Abfälle ist die Vo-raussetzung, auch aus Mahlgut anspruchsvolle Bauteile zu produzieren.
Die Hauptmaterialien sind verschiedene Polyamid-Typen sowie PBT, ABS und Po-lypropylen, alle flammgeschützt modifiziert und mit Glasfasern versetzt. Es werden Materialien mit sehr hohen Glasfaseranteilen von bis zu 60 Prozent verarbeitet.
Für ein homogenes Mahlgut
"Wir haben uns auf der Messe verschiedene Mühlen angeschaut und mit unserem eigenen Material bei den Anbietern Mahlversuche durchgeführt", sagt der Spritz-gießleiter. Im Technikum von Wittmann in Nürnberg wurden die Steckerangüsse auf einer S Max 2 Mühle vermahlen. Das Ergebnis hat überzeugt. Die Mühle lieferte ein sehr homogenes Mahlgut mit Korndurchmessern von 3,5 bis 4 mm und die Staubentwicklung war niedriger als bei anderen Mühlen, die getestet wurden.“
"Die Zahnwalzenmühlenbaureihe S-Max 2 ist auf technische Kunststoffe und schwer zu vermahlende Teile ausgelegt", macht Wolfgang Prütting, Gebietsver-kaufsleiter bei Wittmann Battenfeld Deutschland, deutlich. Selbst bei hohen Glasfaseranteilen erreichen die Mahlwerkzeuge lange Standzeiten.
Die kompakte Bauweise und die eingebaute Schalldämmung sind weitere Plus-punkte, die sich vor allem dann bemerkbar machen, wenn die Mühlen nicht in ei-nem eigenen Raum, sondern direkt in der Produktionshalle betrieben werden.
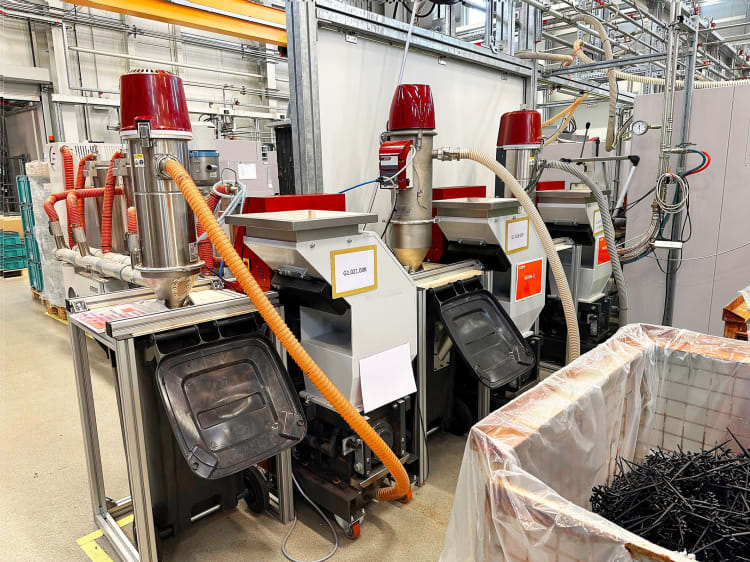
Mahlgut direkt weitertransportieren
Im Standard sind die S-Max 2 Mühlen mit einem Füllstandsensor ausgerüstet. Ist der Auffangbehälter voll, stoppt das Mahlwerk. Um kontinuierlich arbeiten zu kön-nen, hat Wittmann für seinen Kunden eine Sonderlösung realisiert. Statt die Mühle abzuschalten, wird über das Signal des Füllstandsensors ein integriertes Vakuumfördergerät eingeschaltet. Auf diese Weise wird das Material direkt vom Auf-fangbehälter der Mühle in eine Materialtonne transportiert.
Mit der Tonne geht es dann zur großen zentralen Materialversorgungsanlage mit vielen Trocknern, Fördergeräten und einem Kupplungsbahnhof, die eine Etage oberhalb des Lagers angeordnet ist. Die Tonnen mit dem Mahlgut werden mittels Gabelstapler nach oben befördert und mit Gravimax-Dosiergeräten – ebenfalls aus dem Hause Wittmann - verbunden. Die gravimetrische Dosiertechnik erlaubt eine grammgenaue Zudosierung des Mahlguts zur Neuware.
Verbrauch an Neuware deutlich gesunken
Der Verbrauch an Neuware ist seit dem Start des Inhouse-Recyclingprojekts konti-nuierlich zurückgegangen, was unmittelbar in die Stückkosten eingeht und die Wettbewerbsfähigkeit des Produzenten stärkt. In jüngster Zeit sind einige Patente ausgelaufen. Damit verschärft sich der Wettbewerb. "Wettbewerbsfähige Stückkos-ten erreichen wir nur noch mit dem Einsatz von Recyclingmaterial", so der Verarbei-ter. "Die neuen Mühlen hatten sich bereits nach sechs Monaten amortisiert."