Greater efficiency
Efficiency in the filling process includes the brewer being able to determine exactly how much beer the full keg actually contains. In view of the large range of kegs of varying age that arrive from different manufacturers and breweries and are often run in mixed batches, differences in weight of up to two kilograms are no rare occurrence. In order to eliminate this as a source of error, KHS has developed gross tare weighing used on systems for large capacities.
On the Transomat and CombiKeg KHS’ precision filling and measurement system (certified according to the MID for the European market) makes sure that the kegs are racked with the exact required volume of product. Standardized valves for washing and filling, this technology tried and tested on KHS’ bottle fillers, lower the level of complexity, simplify warehousing and trigger fewer faults. They are suitable for both the soiled caustic generated during the first interior washing processes and for the sensitive filling process – without robustness or hygiene being compromised in any way whatsoever.
On the CombiKeg a new exterior washer with optimized multiple use of the washing water earns extra points by saving on resources. The rotary inspection flap facilitates maintenance as it provides easier access to wear parts in the CombiKeg’s rotor shaft.
Improved safety
When deformed or crooked kegs become stuck in the machine, the operator has to intervene. A pressure reducer between the media valves and treatment heads prevents caustic or other liquids from squirting out of the system. This increases safety for the machine operator if, for instance, the machine cladding has to be opened during production – such as when a damaged keg is not properly seated on the treatment head and has to be corrected or removed. The bottom edge of the Plexiglas safety paneling has also been extended for improved shielding and now covers the media valves. As a further option, machines arranged in blocks can also be safely and individually shut down.
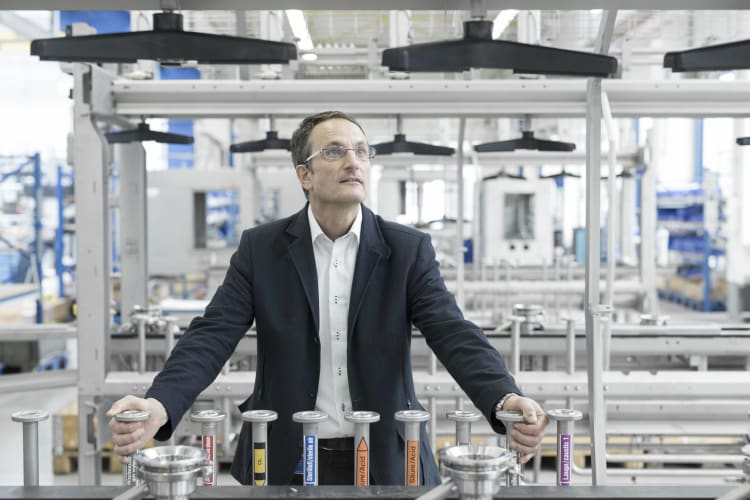
Future-proof network
Thanks to the standard integration of IO-Link the systems are equipped with intelligent sensors and actuators for measuring pressure, for example, or level probes. Signals are provided directly without converters and thus without any of the time loss associated with the latter. Furthermore, a data world is created that permits predictive maintenance in the future, for instance.
Claim to leadership in keg filling
The sheer number of all of these significant further developments underlines the Dortmund machine and systems manufacturer’s claim to leadership also with keg filling systems, Daum believes. “With the above we’re creating an ideal setup that allows our customers to continue filling their beverages into kegs flexibly, efficiently, safely and sustainably in the future, too,” he concludes.